Sherardize is a coat (iron or steel) with zinc by heating it in contact with zinc dust. Sherardising is a process of galvanization of ferrous metal surfaces, also called vapor galvanizing and dry galvanizing. It is a zinc diffusion process for the formation of zinc-iron layers on ferrous work-pieces. It is also known as vapor galvanizing and dry galvanizing is the process of galvanization of ferrous metal surfaces. It is generally used for corrosion protection but is also used as an adhesion promoter.
Sherardising is a zinc coating that when correctly applied gives a uniform, resilient defense against the corrosion of the base metal, making it an ideal process for a number of fasteners and fixings including washers, bolts, nuts, springs, and castings.
The process is named after British metallurgist Sherard Osborn Cowper-Coles (son of naval inventor Cowper Phipps Coles) who invented and patented the method c. 1900. The method involves the heating of the object in an airtight container that has zinc powder. It provides very strong and long-term protection against corrosion and abrasion.
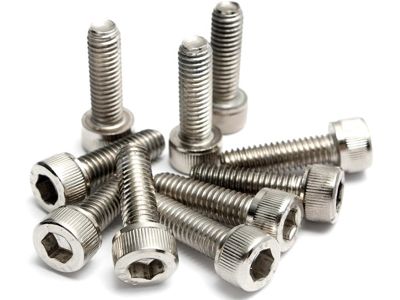
The process involves heating up the steel parts up in a closed rotating drum that also contains metallic zinc dust, and possibly sand. The pre-treated components are placed in a rotating drum with zinc powder and an inert filler, such as quartz sand or corundum. This process involves heating the steel parts up to c. 500°C in a closed rotating drum that contains metallic zinc dust and possibly an inert filler, such as sand. The process provides long term corrosion protection due to the zinc alloy layer. At temperatures above 300°C, zinc evaporates and diffuses into the steel substrate forming diffusion bonded Zn-Fe-phases. By heating, zinc evaporates and diffuses into the metal component to form a firmly adhering zinc-iron alloy with the iron-containing surface.
Sherardising is ideal for small parts and parts that require coating of inner surfaces, such as batches of small items. The coating contains some iron content, making it the hardest and most wear resistant of zinc finishes. Part size is limited by drum size. It is able to withstand damage without loss of performance, and can only be removed by chemical or mechanical means.
Sherardised plating is a highly effective, long term coating which is cost effective due to the initial cost, paired with the pricing of lifetime maintenance and post-treatment. It is reported that pipes up to 6 m in length for the oil industry are sherardised. If the metal surface is free of scale or oxides, no pretreatment is needed. The process is hydrogen-free, hence hydrogen embrittlement is prevented. The external layer of the zinc-iron alloy formed is a pure zinc adherent coating with a smooth surface and uniform thickness.
Information Source: