Silicon nitride (Si3N4) is a chemical compound that combines the elements silicon and nitrogen. Of the silicon nitrides, it is the most thermodynamically stable. As a result, when the phrase “silicon nitride” is used, Si3N4 is the most commercially important of the silicon nitrides. It has a high melting point and appears as a white solid. In the presence of dilute HF and heated H2SO4, it is chemically stable. Metal forming, industrial wear scenarios, and molten metal handling are some of the common applications for this material, which is known for its strong shock and temperature resilience.
The hunt for totally dense, high strength, and high toughness materials led to the development of silicon nitride in the 1960s and 1970s. It’s a white, high-melting-point solid that’s chemically inert, only reacting with dilute HF and hot H2SO4. It is extremely hard (mohs scale 8.5) and has excellent thermal stability. The replacement of metals with ceramics in advanced turbine and reciprocating engines to achieve higher operating temperatures and efficiency was a major driving force behind its development.
It possesses a number of characteristics, including high strength across a wide temperature range, high fracture toughness, high hardness, exceptional wear resistance, and chemical properties. It possesses a remarkable resilience to heat stress. It has a wide range of applications in a variety of fields. In a nitrogen environment, powdered silicon will be heated between 1300°C and 1400°C:
3 Si + 2 N2 → Si3N4
Because some silicon nitrides are very porous, they have a low density and resistance to oxidation. Silicon nitride has good hardness at extremely high temperatures, strong creep resistance, high wear resistance, low coefficient of thermal expansion, chemical resistance, oxidation resistance, and enhanced mechanical strength when appropriately treated. The chemical interaction of silicon and nitrogen causes the weight of the silicon sample to gradually grow. The reaction is complete without an iron catalyst after several hours (~7) when no more weight gain owing to nitrogen absorption (per gram of silicon) is noticed.
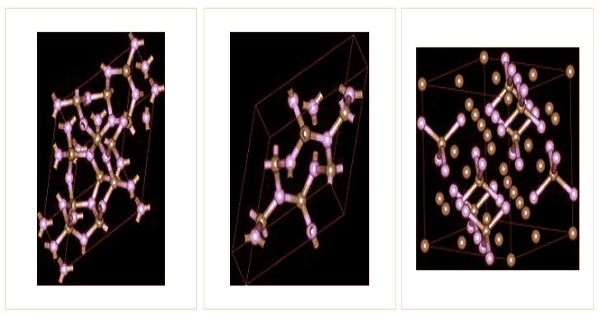
Silicon nitride outperforms most metals at high temperatures, retaining great strength and creep resistance while also resisting oxidation. In addition, as compared to most ceramic materials, its low thermal expansion coefficient provides good thermal shock resistance. Other silicon nitride phases (with chemical formulas corresponding to increasing degrees of nitridation/Si oxidation state) have been documented in the literature, including gaseous disilicon mononitride (Si2N); silicon mononitride (SiN); and silicon sesquinitride (Si2N3), all of which are stoichiometric phases.
It is a key material for engine parts in the vehicle industry. Because of its great shock resistance, it can also be used in the construction of bearings. Silicon nitride ceramic, for example, can withstand the tremendous thermal shock caused by hydrogen/oxygen rocket engines in spacecraft. The products obtained in these high-temperature syntheses, like those acquired in other refractories, are dependent on the reaction circumstances (e.g., time, temperature, and starting materials, including reactants and container materials), as well as the purification method.
Because it dissociates into silicon and nitrogen at temperatures above 1850oC, this covalently linked material does not readily sinter and cannot be heated over that temperature. The diimide method can also be used to make silicon nitride:
SiCl4 + 6 NH3 → Si(NH)2 + 4 NH4Cl(s) at 0 °C
3 Si(NH)2 → Si3N4 + N2 + 3 H2(g) at 1000 °C
Only indirect bonding methods, such as minor chemical additives to promote densification, can be used to produce dense silicon nitride. These substances are referred as as sintering aids, and they typically cause liquid phase sintering. However, using low-purity raw silicon resulted in silicate and iron contamination of silicon nitride.
The diimide breakdown produces amorphous silicon nitride, which must be annealed under nitrogen at 1400–1500 °C to become crystalline powder; this is now the second-most important commercial approach. Silicon nitride cannot be regarded a single material because its qualities are highly dependent on the fabrication procedure. The three main types of silicon nitride are:
- Reaction bonded silicon nitride (RBSN)
- Hot pressed silicon nitride (HPSN)
- Sintered silicon nitrides (SSN)
Carbothermal reduction was the first method for producing silicon nitride and is presently the most cost-effective industrial route to producing high-purity silicon nitride powder. Because of its hardness and wear resistance, it may also be used as an abrasive and cutting tool. It can be utilized as an insulator and chemical barrier in the manufacturing of integrated circuits in electronics. The sol-gel process, which involves carbothermal reduction followed by nitridation of a silica gel containing ultrafine carbon particles, can also be used to make silicon nitride nanowires.
Decomposition of dextrose at temperatures ranging from 1200 to 1350 °C can yield the particles. Silicon nitride creates high-quality components for use in exceptionally demanding applications because it can survive the rigors of severe temperature, mechanical, and wear circumstances. For high-temperature applications, silicon nitride ceramic ball and roller bearings are recommended over steel. For combustion components and wear parts, the greatest market for silicon nitride components is reciprocating (diesel and spark ignited) engines. Because of its hardness, fracture toughness, and thermal shock resistance, silicon nitride is also used in metal cutting tools for cast iron, hard steel, and nickel-based alloys.
Silicon nitride (Si3N4) is utilized in high-temperature crucibles because it is a great covering for metals, as well as an adhesive and abrasive. It’s been found to be a good heat-resistant material for rocket nozzles. Silicon nitride’s corrosion resistance, thermal shock resistance, and thermal conductivity make it ideal for use in the aluminum casting industry. Heating tubes, pump liners, riser tubes, and thermocouple protection sheaths are among them.
The “microshutters” designed for the Near Infrared Spectrograph on the James Webb Space Telescope were made of silicon nitride. Surprisingly, the material has yet to be widely used in gas turbine engines (the initial reason for its invention), owing to the limited availability of small to medium-sized turbine engines. According to NASA:
“The device must be able to work at extremely low temperatures because the operating temperature is cryogenic. Another issue was creating shutters that could open and close frequently without becoming fatigued, open independently, and open wide enough to suit the instrument’s science requirements. Silicon nitride was chosen for use in the microshutters, because of its high strength and resistance to fatigue.”
Information Source: