Lignin is a complex organic polymer that is found in plant cell walls and is typically regarded as a byproduct of processes such as paper and biofuel production. While lignin has significant potential as a renewable material, its use has been limited due to difficulties in effectively separating and processing it. If a cost-effective and efficient lignin separation method could be developed, lignin-based materials could become more profitable, contributing to the growing field of sustainable and renewable materials.
A novel lignin extraction method could aid in the transformation of wheat straw into gold. The new method produced color-neutral, odorless, and homogeneous lignin, which could make this carbon-neutral material a more viable candidate for the development of high-value products.
The Washington State University researchers reported in the Proceedings of the National Academy of Sciences that they extracted up to 93% lignin with up to 98% purity from wheat straw, producing a significant amount of material in a uniform manner that could make it more appealing for industrial use.
“This method allows us to extract lignin from plant material in its native form and at a high yield,” said Xiao Zhang, who led the research at WSU’s Gene and Linda Voiland School of Chemical Engineering and Bioengineering. “We were able to demonstrate to industry that it is possible to make color-neutral and odorless lignin, and we can make quite a bit of the material to begin evaluating its applications.”
This method allows us to extract lignin from plant material in its native form and at a high yield. We were able to demonstrate to industry that it is possible to make color-neutral and odorless lignin, and we can make quite a bit of the material to begin evaluating its applications.
Xiao Zhang
Lignin is the second most abundant renewable carbon source, accounting for approximately 30% of all non-fossil fuel-based carbon on the planet. It is found in all vascular plants, where it forms cell walls and gives the plants rigidity. Lignin supports trees, gives vegetables their firmness, and accounts for 20%-35% of the weight of wood. Although the material has great potential as a precursor for biobased materials and fuels, it is notoriously difficult to extract from plants.
The material is usually separated during papermaking and biorefining, but these processes often contaminate and significantly alter lignin’s chemical and physical properties, decreasing its value. So most lignin is either burned to produce fuel and electricity or used in low-value products, such as for cement additives or as a binder in animal feed. Producing a more homogenous lignin provides the opportunity to pursue high-value material development to replace petroleum-derived plastics and polymers.
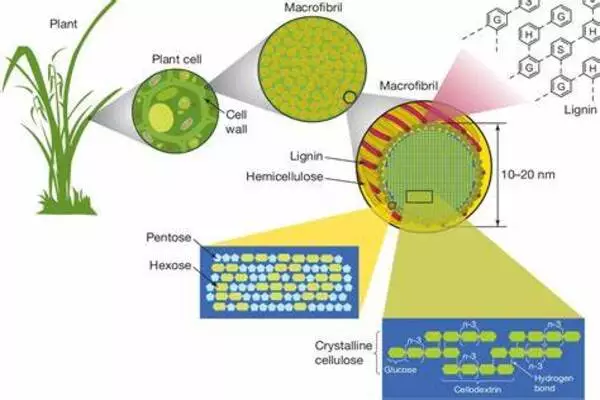
“Despite centuries of effort, lignin cannot be used as a valuable material due to its heterogeneity,” said Zhang, who is also affiliated with Pacific Northwest National Laboratory. “The saying goes, ‘you can make anything out of lignin, except money.’ Nobody can reliably make things out of the molecules because there is so much heterogeneity in them.”
The researchers separated lignin from wheat straw using a solvent and were able to preserve and control its key properties, producing a more uniform molecule with a consistent molecular weight that is more useful for industry. The extracted lignin was light in color, similar to lignin found in nature.
The lignin had a strong affinity for the solvent because it is an electron-rich compound, and the electron interactions allowed the researchers to extract it with minimal chemical reactions, which protected its natural molecular structure, which is frequently damaged in chemical separations.
The Office of Commercialization at WSU has filed a provisional patent and will work with the researchers to scale-up and eventually commercialize this technology. The research team is working to reduce the lengthy processing time and the amount of purification chemicals required to make it more viable for industrial applications.