Ion plating, also known as ion beam deposition, is a surface coating technique used in materials science and engineering to deposit thin films of materials onto various substrates. It is a physical vapor deposition (PVD) technique that involves the use of a high-energy ionized gas (plasma) to deposit the coating material onto the substrate.
It is a physical vapor deposition (PVD) process that is a modified version of vacuum deposition. It is also known as ion assisted deposition (IAD) or ion vapor deposition (IVD). Ion plating involves bombarding the substrate with atomic-sized energetic particles known as ions, which deposit film. Prior to deposition, bombardment is used to sputter clean the substrate surface. During deposition, bombardment is used to modify and control the depositing film’s properties. To maintain an atomically clean interface, the bombardment must be continuous between the cleaning and deposition phases of the process.
Process
The energy, flux, and mass of the bombarding species, as well as the bombarding particle to depositing particle ratio, are all important processing variables in ion plating. The depositing material can be vaporized through evaporation, sputtering (bias sputtering), arc vaporization, or chemical vapor deposition by decomposition of a chemical vapor precursor (CVD). In most cases, the energetic particles used for bombardment are ions of an inert or reactive gas, or in some cases, ions of the condensing film material (“film ions”).
Ion plating can be performed in a plasma environment in which ions for bombardment are extracted from the plasma, or in a vacuum environment in which ions for bombardment are formed in a separate ion gun. The latter ion plating configuration is often called Ion Beam Assisted Deposition (IBAD). By using a reactive gas or vapor in the plasma, films of compound materials can be deposited.
In ion plating, the coating material is first vaporized by heating it in a vacuum chamber. The vaporized material then enters the plasma, where it is ionized and accelerated towards the substrate using an electric field. The high-energy ions collide with the substrate and deposit a thin film of the coating material onto its surface.
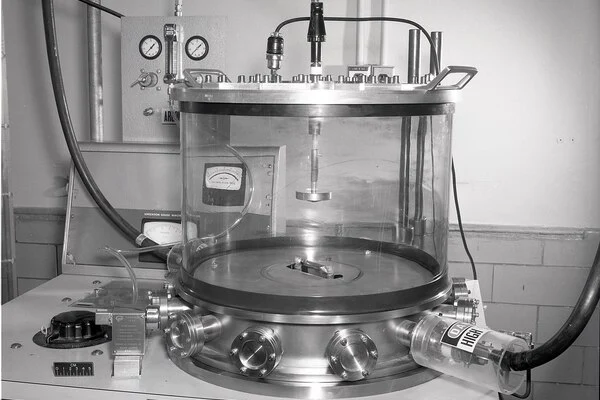
Application
Ion plating is widely used in various industries for applications such as decorative coatings, wear-resistant coatings, and corrosion-resistant coatings. The technique is particularly useful for depositing thin films of materials that are difficult to deposit using other techniques, such as refractory metals, alloys, and ceramics.
Ion plating is also used to deposit hard coatings of compound materials on tools, adherent metal coatings, optical coatings with high densities, and conformal coatings on complex surfaces.
Advantages
One advantage of ion plating over other coating techniques is that it can produce coatings with excellent adhesion and uniformity.
- Better surface coverage than other methods (Physical vapor deposition, Sputter deposition).
- More energy available on the surface of the bombarding species, resulting in more complete bonding.
- Flexibility with the level of ion bombardment.
- Improved chemical reactions when supplying plasma and energy to surface of the bombarding species.
Disadvantages
- Increased variables to take into account when compared to other techniques.
- Uniformity of plating not always consistent.
- Excessive heating to the substrate.
- Compressive stress.