Zinc plating is identical to electro-galvanizing in principle because both are electro-deposition processes. Zinc coatings prevent oxidation of the protected metal by forming a barrier and by acting as a sacrificial anode if this barrier is damaged. It involves the electrodeposition of a thin coating of zinc metal onto the surface of another metal object, known as a substrate. One of the most important benefits of zinc plating is that it will significantly increase the corrosion resistance of the underlying substrate.
Zinc plating is the process of covering substrate metals (like steel and iron, etc.) with a layer or coating of zinc to protect the substrate from corrosion.
Zinc reacts with the oxygen in the atmosphere to form zinc oxide. Zinc oxide is a fine white dust that (in contrast to iron oxide) does not cause a breakdown of the substrate’s surface integrity as it is formed. The zinc oxide subsequently reacts with water to form zinc hydroxide, which bonds with carbon dioxide to produce a thin layer of zinc carbonate. The zinc coating creates a physical barrier that prevents rust from reaching the underlying metal surface.
Indeed, the zinc oxide, if undisturbed, can act as a barrier to further oxidation, in a way similar to the protection afforded to aluminum and stainless steels by their oxide layers. Zinc is chosen because of its innate ability to fight corrosion. Zinc plating can also serve as a protective undercoating prior to painting, as it can promote greater paint adhesion.
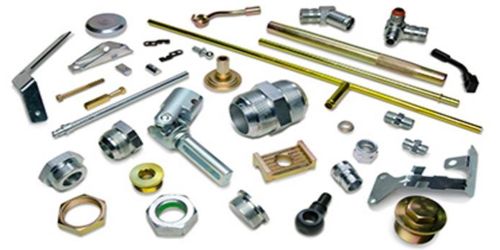
Benefits of Zinc Plating
Zinc coating offers more than excellent protection against corrosion. It is typically used for screws and other small fasteners, light switch plates, and various small parts that will be exposed in interior or mildly corrosive conditions.
- Low cost — Because zinc can be found in abundance, it is viewed as a more cost-effective plating process than when using precious metals such as gold or palladium.
- Increased strength — Although zinc is a relatively lightweight metal, a zinc coating can increase the strength of the substrate.
- Low-stress deposit — Applying a zinc coating will not place an undue amount of stress on a metal part or component.
- Flexibility — Zinc is compatible for use in a wide range of bath chemistries, providing greater flexibility for customizing the plating outcome.
- Ductility — Zinc is an extremely ductile metal, meaning it can be stretched into long, thin strands without breaking.
- High temperature tolerance — Zinc is capable of tolerating temperatures of up to 120° F, which can help lower cooling costs.
Zinc plating is the most commonly used method of galvanization. The majority of hardware parts are zinc-plated, rather than cadmium-plated. Specialized equipment and machinery is also required, including a rectifier, plating station, ancillary tank for proper dissolution of the zinc anode, and a reservoir.
Information Source: