A new study tracked the deposition and removal of lithium metal from a battery anode while it was cycling to figure out how failure happens. The findings could assist improve the usage of pure lithium metal in anodes for electric vehicle batteries, reducing battery weight and drastically increasing driving range.
Pure lithium metal is a viable substitute for graphite-based anodes used in electric vehicle batteries today. It has the potential to significantly reduce battery weight and significantly increase the driving range of electric vehicles when compared to present technologies. However, before lithium metal batteries can be utilized in automobiles, scientists must first figure out how to increase their lifespan.
A recent study led by Peter Khalifah, a scientist at the DOE’s Brookhaven National Laboratory and Stony Brook University, examined lithium metal deposition and removal from a battery anode as it was cycling to identify hints about how failure happens. The discovery was published in a special issue of the Journal of the Electrochemical Society commemorating Nobel Prize-winning battery researcher John Goodenough, who, like Khalifah, is a member of the Battery 500 Consortium research team.
“The rate of lithium plating (deposition) and stripping (removal) in a good battery will be the same at all points on the surface of electrodes,” Khalifah stated. “Our findings indicate that it is more difficult to remove lithium in some locations, implying that there are issues there. By determining the source of the problems, we can devise solutions to eliminate them and create better batteries with bigger capacity and longer lifetimes.”
The work was carried out by Khalifah and his colleagues utilizing strong x-rays at the Advanced Photon Source, a DOE Office of Science user facility at DOE’s Argonne National Laboratory. During a single charge and discharge cycle, they followed lithium as it moved from cathode to anode and back.
Our findings indicate that it is more difficult to remove lithium in some locations, implying that there are issues there. By determining the source of the problems, we can devise solutions to eliminate them and create better batteries with bigger capacity and longer lifetimes.
Peter Khalifah
“The x-rays can look straight through the battery, allowing us to make several measurements very fast to watch what occurs as the battery changes,” Khalifah explained. “To the best of our knowledge, no one has ever used x-rays to map lithium shuttling in real time.”
One difficulty is that lithium atoms are difficult to see with x-rays. The faint signal emitted by the small number of lithium atoms that migrate between the cathode and anode can easily be hidden by stronger signals emitted by other materials in the battery, including the signal emitted by the high amount of lithium on a pure lithium metal anode.
To overcome this issue, Khalifah’s team created a battery cell with a “bare” anode – at least naked in terms of the presence of pre-existing lithium. This enables measuring the signal of the shuttled lithium ions easier. They then conducted a study in which they compared two distinct anode materials – copper and molybdenum – on which lithium ions were deposited as pure lithium metal after being removed from the cathode material during battery operation. The researchers were able to observe how uniformly lithium metal was added to and removed from anode surfaces as a result of this.
Comparing this procedure with copper and molybdenum anodes provided a chance to uncover distinctions between these two metals that could be useful in creating better batteries. The scientists used this configuration to determine how much lithium was present across the electrode while the cell was kept at various stages of charge and discharge.
The maps containing hundreds of data points took roughly an hour to collect. That mapping data could be used to identify changes caused by charging and discharging the battery, but the data collection procedure was too sluggish to be effective for tracking the changes as they happened. To track changes as they occurred, the scientists utilized a faster data gathering approach to repeatedly scan a small fraction of 10 pixel-specific spots during battery cycling.
“We created the maps while the battery was at rest, starting at zero capacity and measuring pixels as we charged to half capacity. Then we paused charging and drew another map before returning to pixel-specific measurements while charging to full capacity. The cell was then discharged while we continued to alternate mapping and pixel scans, pausing to collect maps at half and full discharge” Khalifah elaborated.
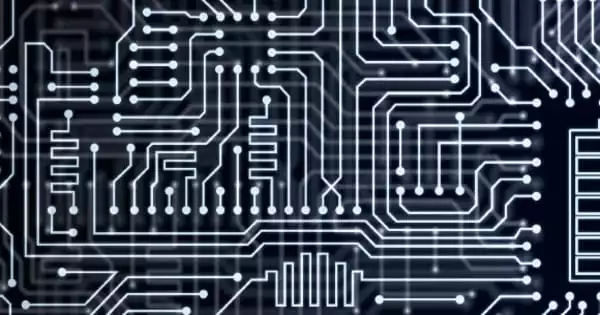
Results reveal variations
All of the spots on the copper anode behaved normally during charging: half of the lithium capacity was deposited on the anode up to the half-charged state, and the full charge state deposited all feasible lithium.
Large discrepancies between pixels emerged during discharge. The lithium was extracted proportionally to the discharge in some pixels (half the lithium was stripped by the half discharge state, and all was gone by full discharge). Other pixels demonstrated a lag in lithium removal, with stripping slow during the first half of discharge and then accelerating to finish the process by full discharge. In some cases, the lagging was so extreme that the majority of the lithium remained on the anode long after the battery had been totally depleted.
“If the lithium is left behind, the cell’s capacity is reduced,” Khalifah explained. “Each lithium atom left behind means one less electron going via the battery’s external circuit. You won’t be able to remove the entire capacity of the cell.”
The discovery that these abnormalities were caused by incomplete lithium extraction was quite surprising. Prior to this discovery, many experts assumed that the main difficulties in lithium metal batteries were caused by lithium plating.
“In general, one would expect it to be more difficult to deposit lithium metal since the atoms must be structured in the precise arrangement of this metal’s crystal structure,” Khalifah noted. “Lithium removal should be simpler because every atom on the surface can be removed without following any precise pattern. Furthermore, if lithium is added faster than the atoms can be deposited uniformly across the surface, the development takes the shape of needle-like dendrites, which can produce electrical shorts (and potentially fires) in the battery.”
The molybdenum anode varied slightly more during plating than the copper anode, but less during stripping.
“Because the lithium behavior was better during the stripping process that created the most overall abnormalities in the anode, it implies that batteries using molybdenum foil substrates rather than copper substrates may provide larger capacity batteries,” Khalifah explained.
However, it is unclear whether the metal choice is responsible for the improved performance of the molybdenum anode. Another aspect could be the distribution of electrolyte, which is the liquid through which lithium ions flow as they shuttle between anode and cathode.
According to the mapping data, the areas of poor performance appeared in locations roughly five millimeters across. The size and shape of such areas, as well as comparisons with other studies, suggest that poor distribution of the liquid electrolyte throughout the battery cell may be to blame for the local loss of capacity in certain places. If this is the case, Khalifah believes that the battery’s performance can be improved by devising a better mechanism for dispersing the electrolyte across the cathode.
“Following-up experiments aimed at distinguishing between metal and solvent effects, as well as testing the effectiveness of strategies for mitigating potential problems such as electrolyte inhomogeneity,” Khalifah said, “will help advance the broader goal of developing high-capacity lithium metal anode batteries with long lifetimes.”