Green hydrogen is hydrogen produced using renewable energy or low-carbon power. Green hydrogen has significantly lower carbon emissions than grey hydrogen, which is produced by steam reforming of natural gas, which makes up the bulk of the hydrogen market.
Engineers in Melbourne have used sound waves to increase green hydrogen production by 14 times using electrolysis to split water. They claim their invention provides a promising way to tap into a plentiful supply of cheap hydrogen fuel for transportation and other sectors, potentially reducing carbon emissions and aiding in the fight against climate change.
The team split the water molecules to release 14 times more hydrogen than standard electrolysis techniques by using high-frequency vibrations to “divide and conquer” individual water molecules during electrolysis.
Electrolysis involves electricity running through water with two electrodes to split water molecules into oxygen and hydrogen gases, which appear as bubbles. This process produces green hydrogen, which represents just a small fraction of hydrogen production globally due to the high energy required.
Our ability to suppress bubble build-up on the electrodes and rapidly remove them through high-frequency vibrations represents a major advance for electrode conductivity and stability. With our method, we may be able to improve conversion efficiency, resulting in a net-positive energy savings of 27%.
Amgad Rezk
Most hydrogen is produced from splitting natural gas, known as blue hydrogen, which emits greenhouse gases into the atmosphere.
Associate Professor Amgad Rezk from RMIT University, who led the work, said the team’s innovation tackles big challenges for green hydrogen production. “One of the main challenges of electrolysis is the high cost of electrode materials used, such as platinum or iridium,” said Rezk from RMIT’s School of Engineering.
“With sound waves making it much easier to extract hydrogen from water, it eliminates the need to use corrosive electrolytes and expensive electrodes such as platinum or iridium. As water is not a corrosive electrolyte, we can use much cheaper electrode materials such as silver.”
The ability to use low-cost electrode materials and avoiding the use of highly corrosive electrolytes were gamechangers for lowering the costs of producing green hydrogen, Rezk said.
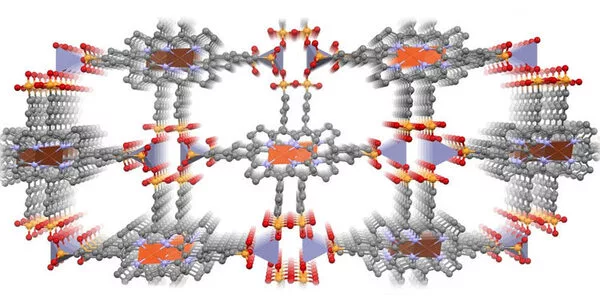
The research is published in Advanced Energy Materials. An Australian provisional patent application has been filed to protect the new technology. First author Yemima Ehrnst said the sound waves also prevented the build-up of hydrogen and oxygen bubbles on the electrodes, which greatly improved its conductivity and stability.
“Electrode materials used in electrolysis suffer from hydrogen and oxygen gas build-up, forming a gas layer that reduces electrode activity and significantly reduces performance,” explained Ehrnst, a PhD researcher at RMIT’s School of Engineering.
As part of their experiments the team measured the amount of hydrogen produced through electrolysis with and without sound waves from the electrical output. “For a given input voltage, the electrical output of electrolysis with sound waves was approximately 14 times that of electrolysis without them. This amounted to the amount of hydrogen produced” Ehrnst stated.
The potential applications of the team’s work
Distinguished Professor Leslie Yeo, one of the lead senior researchers, said the team’s breakthrough opened the door to using this new acoustic platform for other applications, especially where bubble build-up on the electrodes was a challenge.
“Our ability to suppress bubble build-up on the electrodes and rapidly remove them through high-frequency vibrations represents a major advance for electrode conductivity and stability,” said Yeo from RMIT’s School of Engineering. “With our method, we may be able to improve conversion efficiency, resulting in a net-positive energy savings of 27%.”
Next steps
While the innovation appears to be promising, the team must overcome challenges in integrating the sound-wave innovation with existing electrolysers in order to scale up the work. “We are eager to work with industry partners to enhance and complement their existing electrolyzer technology, as well as integrate it into existing processes and systems,” Yeo said.