Caprolactam (CPL) is a colorless to milky white liquid with a slight, unpleasant odor. It has the formula (CH2)5C(O)NH and is an organic chemical. Caprolactam is water-soluble and has a specific gravity of 1.05 (in a 70% solution), making it heavier than water. A lactam (a cyclic amide) of caproic acid is this colorless solid. The bulk of this chemical is used to create Nylon 6 filament, fiber, and polymers, with a global demand of about five million tons per year.
CPL can also be found as a molten substance. Caprolactam is hazardous when inhaled, with a TLV of 5 ppm in vapor and 1 mg/m3 in dust. Skin, eyes, and mucous membranes may be somewhat irritated by contact. Ingestion may cause moderate toxicity. The threat to the environment is the most serious danger. To prevent it from spreading to the environment, immediate action should be done.
Caprolactam was first discovered in the late 1800s when it was made by cyclizing -aminocaproic acid, a result of caprolactam hydrolysis. Synthetic fibers, plastics, film, coatings, and polyurethanes are the most common applications. Caprolactam demand is expected to reach five million tons per year in 2015. Caprolactam is used in the manufacture of filament and fiber, 10% in the manufacture of plastics, and a little amount as a chemical intermediary.
CPL can quickly infiltrate the soil and contaminate groundwater and neighboring waterways because it is a liquid. Many ways for producing caprolactam have been developed due to its commercial importance. It’s a hygroscopic white crystalline substance with a distinct odor. The majority of caprolactam is used to generate nylon 6, which is the raw material for fibers used in the textile and industrial industries.
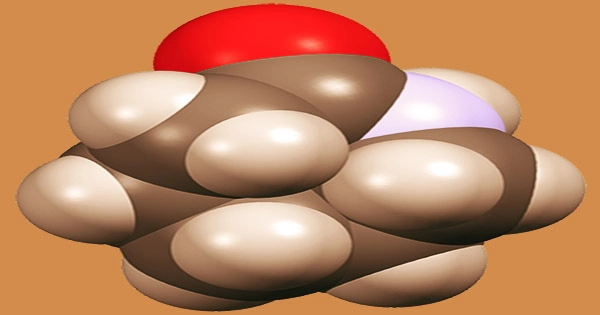
Epsilon-caprolactam is a kind of caprolactam in which the azepane is replaced with an oxo group at position 2. It functions as a metabolite in human blood serum. Caprolactam’s most essential chemical property is polymerization. At 260 to 270°C, the ring is hydrolyzed. Polycondensation is used to create lining polymer chains.
The bisulfate salt of caprolactam is the first result of the acid-induced rearrangement. The free lactam and cogenerate ammonium sulfate are produced when this salt is neutralized with ammonia. Caprolactam also reacts with polymer chains directly through polyaddition. These processes result in a polymer-caprolactam equilibrium that favors a 90 percent conversion to polymer.
When it comes to improving industrial operations, the manufacturing of ammonium salts receives a lot of attention. Caprolactam is the most common basic ingredient used to make polyamide fiber and resin. In the United States, polyamide fiber is known as nylon; in China, it is known as Chinlon because it was originally developed in Jinzhou Petrochemical.
The manufacture of the oxime from cyclohexane using nitrosyl chloride is the other major industrial pathway, accounting for 10% of global production. It is widely used as a solvent and thinner for various paints, paints, inks, and resins, polishes and thinners for leather processing, photographic and magnetic recording material and coating solvent, and so on, due to its strong solubility, low toxicity, and comparatively low price.
Caprolactam is a chemical that is used to make synthetic textiles. Acute (short-term) caprolactam exposure in humans can cause irritation and burning of the eyes, nose, throat, and skin. Because of its simplicity in producing cyclohexanone oximation without the need of hydroxylamine, the newly developed ammoxidation of cyclohexanone has gotten a lot of interest.
Workers exposed to caprolactam through inhalation have reported headaches, lethargy, confusion, and nervous irritability. The Schmidt reaction between cyclohexanone and hydrazoic acid to generate caprolactam has been described on a bench scale. The oxime method’s raw material cyclohexanone can be made by hydrogenating phenol to cyclohexanol and then dehydrating it; or by oxidizing cyclohexane to cyclohexanol and cyclohexanone with the separated cyclohexanol catalytic dehydrogenation yielding ring Pentanone.
Cast nylon is made by in situ anionic polymerization, which involves converting -caprolactam to Nylon 6 inside a mold. Chronic (long-term) exposure of workers to caprolactam has been shown to induce hand peeling and irritation of the eyes, nose, and throat, but no additional health problems. Several pharmaceutical medications, such as pentylenetetrazol, meptazinol, and laurocapram, are made with caprolactam.
Caprolactam did not cause chromosomal abnormalities and aneuploidy in human cells in vitro, but it was not mutagenic in bacterial or in vivo rodent experiments. The United States Clean Air Act of 1990 added it to the list of dangerous air pollutants in 1991. Following the makers’ request, it was removed from the list in 1996.
Caprolactum decomposes and burns, emitting poisonous gases such as nitrogen oxides and ammonia. Brush bristles, textile stiffeners, film coatings, synthetic leather, plastics, plasticizers, paint vehicles, cross-linking for polyurethanes, and lysine synthesis are all examples of caprolactam’s applications. Caprolactam hydrolyzes to aminocaproic acid in water, which is utilized in medicine.
Information Sources: