Zinc-Nickel is a high performance coating that offers exceptional corrosion resistance particularly for parts used in harsh environments. Zinc-nickel plating is one of the best corrosion resistant finishes available offering over 5 times the protection of conventional zinc plating and up to 1,500 hours of neutral salt spray test performance. The development and practical application of electroplated zinc-nickel alloy coatings began during the 1980s, and its acceptance and use have grown slowly but consistently ever since.
Zinc-Nickel is recognized as an environmentally safe alternative to cadmium electroplating. Zinc-nickel platings were developed as a result of increasing requirements with regard to corrosion protection, in particular from the automotive industry, against exposure to temperature, road salt and climatic conditions. It is widely used in the automotive industry to provide corrosion protection for various automotive parts.
Zn-Ni alloy coatings (usually composed of approximately 85% zinc and 15% nickel) are electroplated on carbon steel as a protective coating in a process similar to the way zinc coatings are applied. This plating is a combination of a high-nickel zinc-nickel alloy (10–15% nickel) and some variation of chromate. Zn-Ni coatings typically consist of 8 to 14 µ m layer of 12 to 16% nickel alloy next to the substrate topped by a 0.06 to 0.15 µ m trivalent passivate layer and a 0.5 to 4.0 µ m top coat layer. The most common mixed chromates include hexavalent iridescent, trivalent or black trivalent chromate.
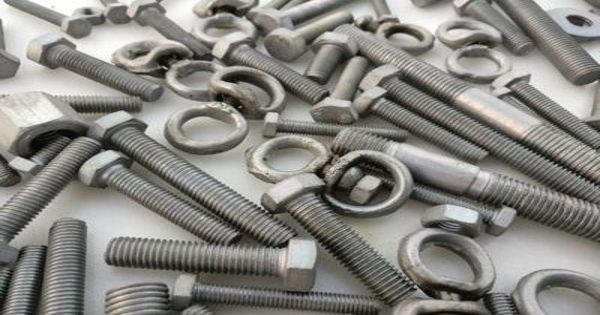
Zinc-Nickel is routinely specified for the following applications: Agricultural Machinery, Heavy Equipment, Oil & Gas, Automotive, Hydraulics, Electrical Transmission, etc. It has also been adopted widely by the aerospace industry and is increasingly being used to protect heavy construction and agricultural equipment, as well as components and devices of all kinds that are exposed to environments that lead to excessive corrosion.
Zn-Ni coatings can provide a much higher degree of substrate protection, which means they can resist the stresses that inevitably shorten the working life of everything from equipment with moving parts to buildings and infrastructure. Used to protect steel, cast iron, brass, copper, and other materials, this acidic plating is an environmentally safe option. Some industries, including automotive and aerospace, have already widely adopted these coatings. Hexavalent chromate has been classified as a human carcinogen by the EPA and OSHA.
Benefits
- Excellent Corrosion Protection – Up to 10 times more protection than conventional zinc.
- Ideal for outdoor use or parts subject to harsh environments.
- A ductile coating that maintains good adhesion after post-plate forming or bending.
- Limits thermal stress to parts subjected to high temperatures.
- Heat resistant and can maintain good corrosion protection after being exposed to high temperatures.
Information Source: