Hokkaido University researchers have successfully developed a new method for imbuing generic polymers with luminescent properties, such as polystyrene and polyethylene. The technique, which was published in the journal Angewandte Chemie International Edition, allows for the simple preparation of luminescent polymers without the use of complex organic synthetic methods.
“Luminescent polymers are widely used in modern society, in applications such as organic lasers, solar cells, sensors, and bioimaging, but their preparation often requires multiple chemical synthesis steps, which are both time and labor intensive,” explains Professor Hajime Ito, one of the study’s authors and Vice Director of the Institute for Chemical Reaction Design and Discovery (WPI-ICReDD).
Hokkaido University researchers have developed a simple method that converts existing generic polymers into luminescent polymers using mechanical force, such as polystyrene and polyethylene.
To address this issue, the researchers investigated whether luminescent polymers could be synthesized using mechanical force rather than sophisticated chemical synthesis.
“It is well known that mechanically stimulating polymers, such as grinding or crushing them, generates reactive species known as free radicals,” says paper co-author Associate Professor Koji Kubota of Hokkaido University. “Inspired by this phenomenon, as well as our previous research into mechanical-force-induced luminescence and reactions, we wanted to see if we could develop a simpler method for producing functional luminescent materials.”
Afterglow imaging with long-lasting luminescence after light excitation provides opportunities for ultrasensitive molecular imaging; however, exploitation in clinical settings has been hampered by a lack of biologically compatible afterglow agents.
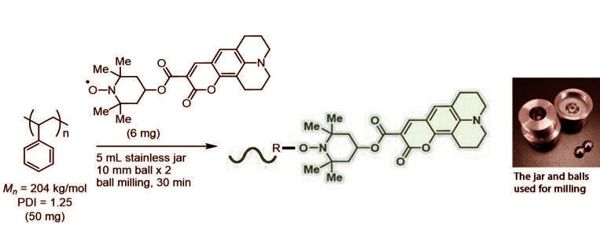
In this study, the polymer and pre-fluorescent radical reactants were combined in a ball milling jar with stainless steel balls. The jar was then shaken, which caused the balls to grind the solid compounds and start a reaction. The covalent bonds in the polymer chains were cleaved during this process, and the pre-fluorescent molecules were inserted into the polymer, resulting in significantly higher emission intensity. This method was successfully applied to polystyrene, polyethylene, polyphenylene sulfide, polysulfone, and other generic polymers by the researchers.
“With further development,” says Hokkaido University Assistant Professor Mingoo Jin, “the method could potentially be adapted to introduce other functions to generic polymers.”
“We hope to use this method in the future to develop novel sensing and recording materials that change color in response to mechanical stimuli,” Hajime Ito added. This could pave the way for “smart” materials to be used in a variety of applications, including bioimaging reagents and pressure-sensitive sensors.
Polymers are abundant in nature. The deoxyribonucleic acid (DNA) and ribonucleic acid (RNA) that define life are the ultimate natural polymers. Protein polymers include spider silk, hair, and horn. Starch, like cellulose in wood, can be a polymer. Latex and cellulose from rubber trees have been used as raw materials in the production of manufactured polymeric rubber and plastics. Bakelite was the first synthetic manufactured plastic, developed in 1909 for telephone casings and electrical components. Rayon, made from cellulose, was the first manufactured polymeric fiber in 1910. Nylon was invented in 1935 while attempting to create synthetic spider silk.