While anthropogenic CO2 emissions continue to rise, recycling carbon dioxide (CO2), particularly through conversion to methane (CH4), is compelling. Photothermal methanation is a useful process for this transformation, in which CO2 and hydrogen are catalytically converted into CH4 and water when exposed to sunlight. A team of researchers has now reported the synthesis of a highly active, stable nickel-carbon catalyst for this reaction in the journal Angewandte Chemie.
According to the study, a method developed by researchers at the US Department of Energy’s Pacific Northwest National Laboratory (PNNL) for converting captured carbon dioxide (CO2) into methane could significantly reduce carbon capture costs.
The researchers were able to extract CO2 from power plant flue gas using a solvent known as EEMPA before binding it and converting it into useful chemicals such as methane. This method was discovered to be significantly less expensive than the existing methane conversion process. The study discovered that the initial investment cost was 32% lower, the operation and maintenance costs were 35% lower, and the overall selling price of synthetic natural gas was 12% lower.
The methane produced by this process, which uses waste CO2 and renewable hydrogen, could provide an alternative for utilities and consumers seeking natural gas with a renewable component and a lower carbon footprint.
Luis Garzón-Tovar and Jorge Gascon
The team at King Abdullah University of Science and Technology (Thuwal, Saudi Arabia) led by Luis Garzón-Tovar and Jorge Gascon was looking for an efficient, cost-effective catalyst for photothermal methanation of CO2. The combination of light-driven and thermal chemical processes underpins photothermal catalysis. Unlike pure photocatalysis, it allows longer wavelength light in the visible and infrared regions of the spectrum to contribute to driving the reaction.
Instead of precious metals, they chose a high load of nickel nanoparticles on a carbon-based support to base the new catalyst on an abundant, inexpensive metal. Carbon materials are highly promising photothermal catalysis supports because they absorb a wide range of light, are highly efficient at converting light to heat energy, and have a large surface area.
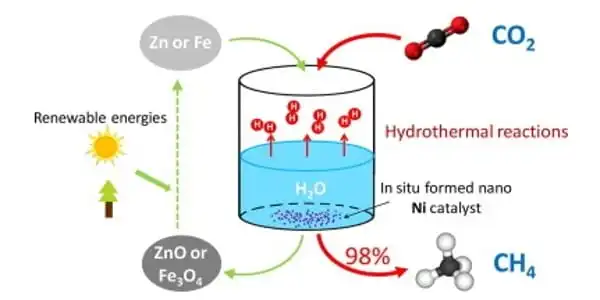
The catalyst was created using a nickel-containing metal-organic framework (Ni-MOF-74) as the starting material. This material performed best when pyrolyzed under controlled conditions at 600°C. When Ni-MOF-74 decomposes, it leaves behind uniformly finely distributed nickel nanoparticles embedded in a porous graphitic carbon matrix. Under artificial UV, visible, and infrared light, the resulting material, dubbed Ni@C, demonstrated a high rate of conversion and high selectivity for methanation. The efficiency of the catalyst remained stable over a period of more than 12 hours in a continuous process in a flow-type reactor.
An experiment was conducted outside, under natural sunlight, to demonstrate the system’s practical application, demonstrating the potential of this new catalyst to reduce CO2 to CH4 using solar energy.
“The methane produced by this process, which uses waste CO2 and renewable hydrogen, could provide an alternative for utilities and consumers seeking natural gas with a renewable component and a lower carbon footprint.”
EEMPA also allows for easy CO2 dissolution when capturing the gas emitted by plant chimneys. The captured CO2 can then be converted on-site to methane by combining it with renewable hydrogen and a catalyst inside a chamber. The mixture is then heated to half the pressure required by traditional CO2 to methane conversion methods, further reducing the energy required.
Because methanol has many more practical applications than methane, the research team intends to apply the same process that works for methane to methanol. The team is also looking into the possibility of using captured CO2 to make plastics.
According to the authors’ analysis, additional cost savings can be realized because CO2 captured by EEMPA can be converted to methane on-site. CO2 is traditionally extracted from water-rich solvents and transported off-site to be converted or stored underground. Captured CO2 can be mixed with renewable hydrogen and a catalyst in a simple chamber, then heated to half the pressure used in traditional methane production methods.
The reaction is efficient, according to the authors, converting more than 90% of captured CO2 to methane, though the final greenhouse gas footprint depends on what the methane is used for. Furthermore, EEMPA captures more than 95 percent of CO2 emitted in flue gas. The new process also generates excess heat, which is used to generate steam for power generation.