organization for space In order to create its mission hardware, NASA has begun using artificial intelligence. The result, according to NASA, is components that are two-thirds lighter and significantly stronger than their human-designed equivalents.
The research engineer Ryan McClelland-developed Evolved Structures method uses a generative algorithm to produce metal brackets and mounts for various space travel projects in a fraction of the time required by NASA’s expert designers.
On NASA’s Small Steps, Giant Leaps podcast, McClelland said that if things are working well, humans might iterate once every two weeks or so.
“The Algorithm will work at a rate of about one iteration per minute. As a result, you get a lot more iteration cycles, and as a result, you simply get more optimal designs much, much quicker.”
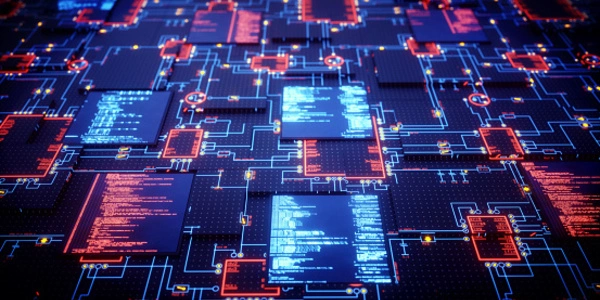
NASA is using artificial intelligence to build parts for its EXCITE telescope and spectrometers (above)
The technology has so far been used to create everything from a scaffold for NASA’s EXCITE telescope mounted on a balloon to an optical bench for an ultraviolet imaging spectrometer to support its optical components.
The optical bench is most likely the most impressive of the present applications, McClelland told Dezeen.
“It is a significant improvement over conventional optical benches in terms of structural function. Additionally, it reduced what would have been roughly ten components to a single part that is still capable of being CNC machined.”
The system still depends on human input in the form of a detailed brief that specifies the requirements for the part, including the load it must bear and the forces to which it will be subjected, much like the ChatGPT chatbot or the image generator DALL-E.
This information is used to feed the generative design software, which can create 30 to 40 versions in a matter of hours, each of which improves on the previous one to create an ideal structure.
“The AI comes up with the design, and then tests the design by finite element analysis to make sure it works, to verify the requirements and then it also does a fabrication simulation to make sure it can be fabricated,” McClelland stated on the show.
This implies that the finished design can be machined by a typical CNC mill using the CAD model directly in a digital manufacturing process.
This procedure can take as little as one week from design to production. According to McClelland, that is approximately ten times quicker than NASA’s standard procedure, which includes passing the design back and forth between a designer, a stress analyst who evaluates its performance, and a machinist who determines whether it can be produced.
“What the Evolved Structures process does is collapse that back and forth that goes on between a few different people – and can take months or years depending on the project, how dedicated the individuals are, and whether they’re working on other things,” he said.
The resulting parts have “almost bone-like” organic forms that can withstand greater structural loads than human-made parts.
McClelland discovered that the components created by AI have up to ten times reduced stress concentrations while weighing up to two-thirds less.
He claimed, “The structures tend to function much better. “Their performance is somewhere around three times greater.”
McClelland predicts that the design process will become standard practice when building structural parts, electronics, and other subsystems within NASA’s instruments and spacecraft gave that the agency produces thousands of custom parts each year for its various missions.
In turn, this would aid in cutting the time and expense involved in space research.
He said, “The space station accommodates six or seven people, but it costs $100 billion. Because AI is so good at this kind of activity, “I really believe it has the potential to dramatically lower the cost of developing these complex systems.”
A rocket engine prototype that was 3D-printed in one piece was previously created by the German software firm Hyperganic using artificial intelligence.