Thermal spraying is a technology that improves or restores the surface of a solid material. Thermal spraying techniques are coating processes in which melted (or heated) materials are sprayed onto a surface. The process can be used to apply coatings to a wide range of materials and components, to provide resistance to – wear, erosion, cavitation, corrosion, abrasion, or heat. The “feedstock” (coating precursor) is heated by electrical (plasma or arc) or chemical means (combustion flame). Thermal spraying is also used to provide electrical conductivity or insulation, lubricity, high or low friction, sacrificial wear, chemical resistance, and many other desirable surface properties.
All methods of thermal spraying involve the projection of small softened particles onto a cleaned and prepared surface where they adhere to form a continuous coating. Thermal spraying can provide thick coatings (approx. thickness range is 20 microns to several mm, depending on the process and feedstock), over a large area at a high deposition rate as compared to other coating processes such as electroplating, physical and chemical vapor deposition. Thermal spray coatings are extensively used in the manufacturing of gas turbines, diesel engines, bearings, journals, pumps, compressors, and oil field equipment, as well as coating medical implants.
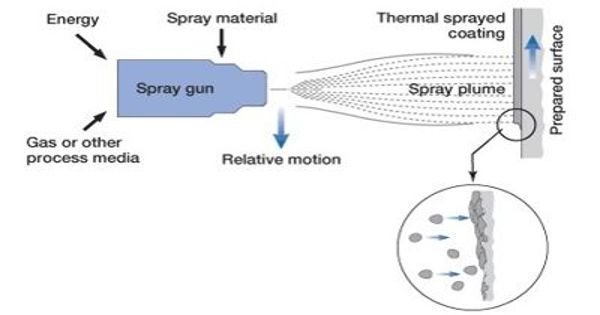
Thermal spraying is a generic category of coating processes that apply a consumable as a spray of finely divided molten or semi-molten droplets to produce a coating. Coating materials available for thermal spraying include metals, alloys, ceramics, plastics, and composites. It is distinguished by its ability to deposit coatings of metals, cermets, ceramics, and polymers in layers of substantial thickness, typically 0.1 to 10mm, for engineering applications. They are fed in powder or wire form, heated to a molten or semi-molten state, and accelerated towards substrates in the form of micrometer-size particles. At the substrate surface, the particles form ‘splats’ or ‘platelets’ that interlock and build up to give the coating.
Thermal spraying is widely adopted across many industries as a preferred method. Combustion or electrical arc discharge is usually used as the source of energy for thermal spraying. It has huge scope to extend the life of new components or through the use of tried and tested techniques, to repair and re-engineer worn or damaged components. The resulting coatings are made by the accumulation of numerous sprayed particles. The surface may not heat up significantly, allowing the coating of flammable substances.
Thermal spraying processes have been widely used for many years throughout all the major engineering industry sectors for component protection and reclamation. Coating quality is usually assessed by measuring its porosity, oxide content, macro and micro-hardness, bond strength, and surface roughness. Recent equipment and process developments have improved the quality and expanded the potential application range for thermally sprayed coatings. Generally, the coating quality increases with increasing particle velocities.
Information Source: