Researchers developed a new design for thermal actuators that can be used to generate rapid movement in soft robotic devices. They use thermal actuation “is not new for soft robots,” but the most difficult part for soft thermal actuators was that they were somewhat unhurried, and these North Carolina State University scientists have transformed them to become fast.
Soft robotics is a branch of robotics that deals with the design, control, and fabrication of robots made of compliant materials rather than rigid links. North Carolina State University researchers have developed a new design for thermal actuators, which can be used to create rapid movement in soft robotic devices. Actuators, in essence, are components of a device, such as a space robot, that generate motion by converting energy into work. According to the paper’s first author, Shuang Wu, a Ph.D. student at NC State, the structure with a bi-stable design is what makes the new actuator design work.
“Using thermal actuation is not new for soft robots, but the biggest challenge for soft thermal actuators was that they were relatively slow and we’ve made them fast,” says Yong Zhu, corresponding author of the paper and the Andrew A. Adams Distinguished Professor of Mechanical and Aerospace Engineering at NC State.
Using thermal actuation is not new for soft robots, but the biggest challenge for soft thermal actuators was that they were relatively slow and we’ve made them fast. Potential applications range from biomedical applications to prosthetic devices to high-end manufacturing.
Yong Zhu
“What makes this new actuator design work is a structure with a bi-stable design,” says Shuang Wu, first author of the paper and a Ph.D. student at NC State. “Consider a hair clip with a snap. It’s stable until you apply a certain amount of energy (by bending it over), at which point it snaps into a different shape that’s also stable.”
In the case of the new thermal actuator, the material is bi-stable, but temperature determines which shape the material prefers. This is how it works. Two materials are layered on top of each other, with silver nanowires in the middle. Because the coefficients of thermal expansion of the two materials differ, they expand at different rates as they heat up. In practice, this means that the structure bends when heated.
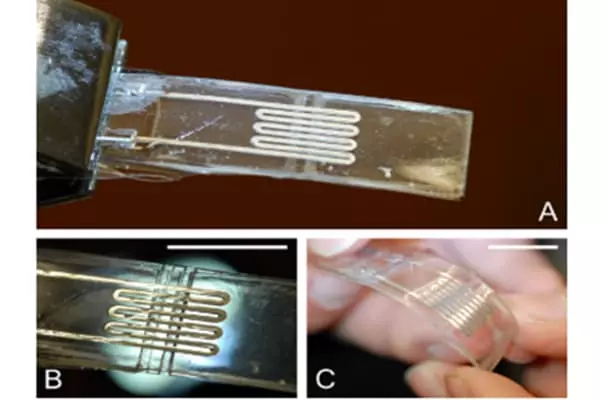
This layered material is then formed into a design that gives it a default curvature in one direction, say downward. When a voltage is applied to the silver nanowires, they heat up and bend in the opposite direction. When a certain temperature is reached – the critical temperature – the material snaps into its new default shape, curving up rapidly. When the voltage is removed, the temperature returns to normal. When the material cools below another critical temperature, it snaps back to its previous default shape, curving down rapidly. It is worth noting that the two critical temperatures differ; the first is higher. You can make the material snap back and forth by applying current to the nanowires in a regular pattern.
Two prototypes were created by the researchers to demonstrate the technique. One of the prototypes mimics the snapping behavior of a Venus flytrap, while the other is a “crawler” capable of moving more than one body length per second.
“Potential applications range from biomedical applications to prosthetic devices to high-end manufacturing,” Zhu says. “Any application in which you want to be able to move quickly while avoiding rigid materials and conventional robotics.”
The next step is to create sensor and control mechanisms that can fully automate the actuation process, allowing it to operate more efficiently than purely manual controls. “We’re also interested in looking into other materials to fine-tune the thermal and mechanical properties,” Zhu says. “We may be able to tailor both actuator speed and force as a result of this.”
Notably, the critical temperatures are not the same. The first is, by far, the most important. The material can be made snapping back and forth by applying current to the nanowires in a standard pattern. The study’s authors created two prototypes to demonstrate such an approach. One of them mimics the snapping behavior of a Venus flytrap, while the other is a “crawler” capable of moving more than a single body length per second.
Potential applications, according to Zhu, range from “biomedical applications to prosthetic devices to high-end manufacturing.” Furthermore, any application in which one would like to be able to move quickly while avoiding rigid materials and traditional robotics. The development of sensors and the regulation of mechanisms that could more completely automate the actuation process, allowing it to operate more efficiently than purely manual regulators, are the next steps.
Zhu explained in their paper that they are also interested in exploring other possible materials so that they can fine-tune the thermal and mechanical properties. They may be able to tailor both the speed and force of the actuator as a result of this.