OLED is a new display technology that allows for stunning and energy-efficient screens and lighting panels. OLEDs are already utilized in smartphones, laptops, wearables, tablets, and televisions, and many of them are flexible. An OLED’s plastic, organic layers are thinner, lighter, and more flexible than an LED’s or LCD’s crystalline layers.
Researchers at the University of Minnesota Twin Cities utilized a modified printer to fully 3D print a flexible organic light-emitting diode (OLED) display in a pioneering new study. The breakthrough could lead to low-cost OLED displays that can be mass-produced at home using 3D printers rather than by technicians in expensive microfabrication facilities in the future.
The technology behind OLED displays is based on the conversion of power into light via an organic material layer. OLEDs are high-quality digital displays that can be made flexible and used in both large-scale devices like television panels and monitors and portable electronics like smartphones. OLED displays have grown in popularity because to its lightweight, low power consumption, thin and flexible design, and wide viewing angle, and excellent contrast ratio.
The device displayed rather consistent emission across the 2,000 bending cycles. This suggests that fully 3D printed OLEDs can potentially be exploited for crucial applications in soft electronics and wearable devices.
Michael McAlpine
“OLED displays are typically created in large, expensive, ultra-clean fabrication facilities,” said Michael McAlpine, the senior author of the study and a University of Minnesota Kuhrmeyer Family Chair Professor in the Department of Mechanical Engineering. “We wanted to test whether we could basically condense all of that down and print an OLED display on our custom-built table-top 3D printer, which costs approximately the same as a Tesla Model S.”
The team has previously attempted to 3D print OLED panels, but they were frustrated by the uniformity of the light-emitting layers. Other groups used spin-coating or thermal evaporation to deposit specific components and produce functional devices in addition to partially printing displays.
The University of Minnesota research team utilized two different types of printing in this new work to print the six device layers, resulting in a completely 3D-printed, flexible organic light-emitting diode display. The electrodes, interconnects, insulation, and encapsulation were all extrusion printed, while the active layers were spray printed at room temperature on the same 3D printer. The display prototype contained 64 pixels on each side and measured roughly 1.5 inches on each side. Every pixel was functional and displayed light.
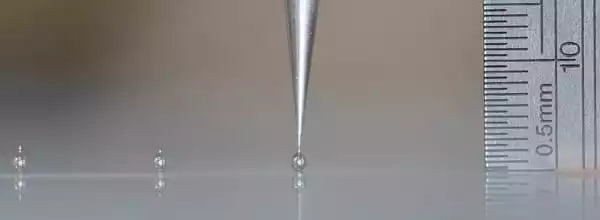
“I expected something, but not a fully functional display,” said Ruitao Su, the study’s first author and a 2020 University of Minnesota mechanical engineering Ph.D. graduate who is now a postdoctoral researcher at MIT. “But then I discovered that all of the pixels were operational, and I was able to display the text I had created. My first thought was, ‘It’s genuine!’ I couldn’t sleep the entire night.”
Su added that the 3D-printed display was also flexible and could be packaged in an encapsulating material, making it suitable for a wide range of applications. “The device displayed rather a consistent emission across the 2,000 bending cycles,” Su said. “This suggests that fully 3D printed OLEDs can potentially be exploited for crucial applications in soft electronics and wearable devices.”
The next stage, according to the experts, is to 3D print OLED panels with higher resolution and improved brightness. “The good thing about our study is that the manufacturing is all built-in, so we’re not talking about 20 years out with some ‘pie in the sky’ vision,” McAlpine explained. “This is something that we actually created in the lab, and it’s not difficult to envisage translating this to creating all kinds of displays yourself at home or on the road in a matter of years, using a little portable printer.”
In addition to McAlpine and Su, the research team included Xia Ouyang, a postdoctoral researcher at the University of Minnesota; Sung Hyun Park, who is now a senior researcher at Korea Institute of Industrial Technology; and Song Ih Ahn, an assistant professor of mechanical engineering at Pusan National University in Korea.
The research was financed primarily by the National Institutes of Health’s National Institute of Biomedical Imaging and Bioengineering, with additional funding provided by The Boeing Company and the Minnesota Discovery, Research, and InnoVation Economy (MnDRIVE) Initiative of the State of Minnesota. Parts of this research were carried out at the Minnesota Nano Center, which is funded by the National Science Foundation under the National Nano Coordinated Infrastructure Network (NNCI).