Modular self-reconfiguring robotic systems or self-reconfigurable modular robots are autonomous kinematic machines with variable morphology. The field of modular self-reconfigurable robotic systems addresses the design, fabrication, motion planning, and control of autonomous kinematic machines with variable morphology. The researchers in the robotics domain identified various applications and prototyped numerous robotic models while addressing constraints such as homogeneity, reconfigurability, form factor, and power consumption. Most of the traditional robotic solutions are operated in a controlled environment and any changes in environments often make these traditional solutions inflexible due to lack of their adaptive nature.
The field of modular self-reconfigurable robotic systems addresses the design, fabrication, motion planning, and control of autonomous kinematic machines with variable morphology.
Modular self-reconfigurable systems have the promise of making significant technological advances to the field of robotics in general. Beyond conventional actuation, sensing and control typically found in fixed-morphology robots, self-reconfiguring robots are also able to deliberately change their own shape by rearranging the connectivity of their parts, in order to adapt to new circumstances, perform new tasks, or recover from damage. The diversified nature of various modular robotic solutions proposed for real-world applications and utilization of different sensor and actuator interfacing techniques along with physical model optimizations presents implicit challenges to researchers while identifying and visualizing the merits/demerits of various approaches to a solution.
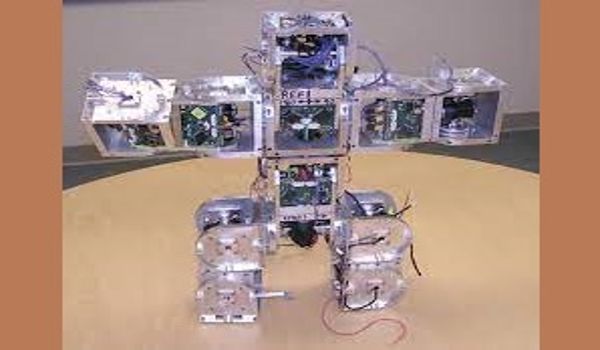
Modular self-reconfigurable robots present wide and unique solutions for growing demands in the domains of space exploration, automation, consumer products, and so forth. For example, a robot made of such components could assume a worm-like shape to move through a narrow pipe, reassemble into something with spider-like legs to cross uneven terrain, then form a third arbitrary object (like a ball or wheel that can spin itself) to move quickly over fairly flat terrain; it can also be used for making “fixed” objects, such as walls, shelters, or buildings. The higher utilization factor and self-healing capabilities are the most demanded traits in robotics for real-world applications and modular robotics offer better solutions in these perspectives in relation to traditional robotics.
In some cases this involves each module having 2 or more connectors for connecting several together. Modular robotics provides a unique advantage over traditional robotic technologies in terms of reconfigurability, reusability, and ease in manufacturing. They can contain electronics, sensors, computer processors, memory, and power supplies; they can also contain actuators that are used for manipulating their location in the environment and in relation to each other. The traditional robotic designs such as robotic arms and hexapods. provide unique solutions to each real-world application and the generated prototypes are generally inflexible for the rest of the applications.
Information Source: