Eco-friendly fabrication of high-efficiency chalcopyrite solar cells can be achieved through a variety of methods. One approach is to use low-cost, non-toxic materials in the fabrication process, such as replacing toxic solvents with water-based solutions. Another approach is to use sustainable energy sources, such as solar or wind power, to power the fabrication process. Additionally, recycling and reusing materials can also help to reduce the environmental impact of the fabrication process. The use of efficient processes and equipment to minimize the use of resources and energy, as well as minimizing waste can also be considered.
Clean, sustainable energy solutions are required to meet the world’s ever-increasing energy demands. Solar cells with high efficiency are promising candidates for reducing carbon emissions and achieving carbon neutrality. In this regard, solution-processed copper indium gallium sulfur diselenide solar cells (CIGSSe) have sparked considerable interest due to their excellent photovoltaic properties, such as high visible light absorption, stability, and tunable bandgap. However, large-scale, practical applications are hampered by a two-pronged problem.
When compared to expensive, vacuum-based fabrication methods, the power conversion efficiency (PCE) of solution-processed copper indium gallium sulfur diselenide solar cells is significantly lower. Furthermore, solution-based methods rely on hazardous solvents. To that end, researchers at Incheon National University in Korea have developed a low-cost, environmentally friendly fabrication technique that does not require a vacuum. This novel approach produces a relatively high PCE of more than 17%.
We carried out spray deposition in an air environment without using any high vacuum facility, which significantly reduces fabrication cost and thus makes the fabrication technique more practical and competitive in the industry sector.
Prof. JunHo Kim
For starters, solution-based CIGSSe fabrication has a very low power conversion efficiency and frequently employs non-environmentally friendly solvents. Second, in order to achieve higher power conversion efficiency, fabrication methods rely on an expensive vacuum environment, which results in significant material loss. To that end, a group of researchers led by Professor JunHo Kim of the Global Energy Research Center for Carbon Neutrality at Incheon National University in Korea developed a low-cost and environmentally friendly method of fabricating high-efficiency CIGSSe solar cells.
In a study made available online and subsequently published in volume 32 Issue 46 of Advanced Functional Materials, the researchers used aqueous spray deposition in an air environment and developed a CIGSSe solar cell with power conversion efficiency (PCE) larger than 17 %. “For spray solution, we used deionized water, which is eco-friendly and the cheapest solvent till date,” explains Prof. Kim. Moreover, conventional solution-based fabrication processes rely on environmentally hazardous, cadmium-based buffers for the optimization of thin-film solar cells. In this novel technique, the researchers used indium sulfide-based buffer that is a cadmium-free, eco-friendly alternative.
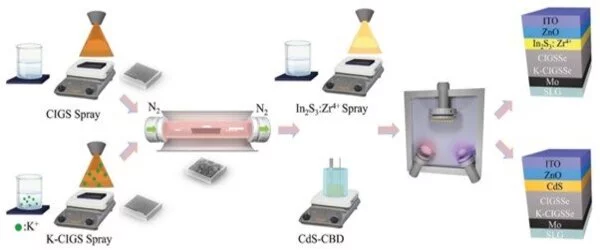
The researchers went on to investigate zirconium alloying effects on indium sulfide buffers. Surprisingly, the team discovered that zirconium alloying raises the electron concentration in the buffer. Furthermore, this method “passivates” or reduces defect states in the CIGSSe absorber, optimizing charge transfer between different interfaces and resulting in improved PCE. By alloying the CIGSSe absorber with potassium, the researchers were able to achieve even more defect passivation and a higher PCE of more than 17%. The manufactured cell has an optimal bandgap for high-efficiency applications such as bottom or tandem cells.
Because it does not require a vacuum environment, this novel technique is both cost-effective and easily scalable. “We carried out spray deposition in an air environment without using any high vacuum facility,” says Prof. Kim, “which significantly reduces fabrication cost and thus makes the fabrication technique more practical and competitive in the industry sector.”
This advancement improves both the performance and the fabrication of CIGSSe solar cells. This will change the way these cells are used in integrated photovoltaic devices and vehicle-integrated photovoltaic devices, as well as energy sources for internet of things devices.