Autoclaved aerated concrete (AAC) is a precast, lightweight foam concrete building material that can be used to make concrete masonry unit (CMU) blocks. In the 1920s, a Swedish architect mixed the traditional concrete mixture of cement, lime, water, and sand with a small amount of aluminum powder for the first time. AAC, which was invented over 800 years ago, provides structure, insulation, and fire and mold resistance all at the same time. Blocks, wall panels, floor and roof panels, cladding (façade) panels, and lintels are examples of types.
AAC concrete is usually formed into blocks or slabs and used to create mortared walls in the same way as regular concrete blocks are. The intensity of blocks normally ranges from 3 to 9 Nmm-2 (when tested). Densities range from about 460 to 750 kg m-3; for comparison, medium density concrete blocks have a typical density range of 1350-1500 kg m-3 and dense concrete blocks a range of 2300-2500 kg m-3. AAC products can be used for both interior and exterior construction, and they can be covered with siding materials like veneer brick or vinyl siding or painted or coated with a stucco or plaster compound to protect them from the elements.
Cellular concrete has been tackling the quest for an industrial material with characteristics identical to wood since its discovery in 1920. It was light, could be cut or perforated, and avoided some of its drawbacks, such as water absorption and maintenance requirements. ACC products can be routed, sanded, or cut to size on site using regular power tools and carbon steel cutters, in addition to being simple and easy to install. Autoclaved Aerated Concrete (AAC) blocks are now widely available, thanks to companies like Hebel and Retak, which are developing a simple and effective construction method.
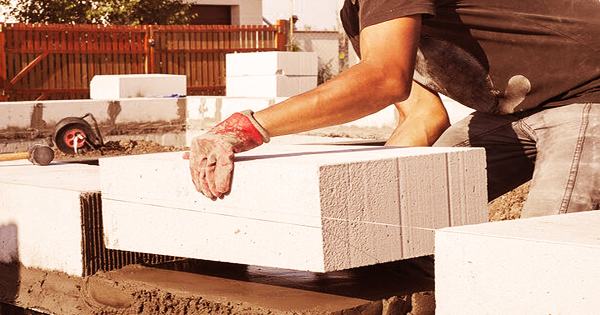
Autoclaved aerated concrete (AAC) blocks are used to shape the inner leaf of a cavity wall and are excellent thermal insulators. They’re often used in foundations and the outer leaf, where they’re normally rendered. Walls, floors with reinforced aircrete beams, ceilings, and the roof can all be built from autoclaved aerated concrete. Aerated concrete that has been autoclaved can be quickly cut to any form. Aircrete is sold under a variety of brand names, much like other masonry products. Aircrete has good acoustic properties and is long-lasting, with good resistance to sulfate attack, fire, and frost damage.
Unlike most other concrete applications, AAC is made with only sand as an aggregate. Binding agents include quartz sand, calcined gypsum, lime (mineral), and/or cement, as well as water. Air bubbles are introduced in the material as aluminum is used as an expansion agent, resulting in a low-density lightweight material. Wet concrete is formed into shapes using templates, then partially dried slabs and blocks are removed. Aluminum powder is used at a concentration of 0.05–0.08% by volume (depending on the pre-specified density). Fly ash from coal-fired power plants with a silica content of 50–65 percent is used as an aggregate in certain countries. AAC concrete units are easy to work with and can be cut and drilled with common woodworking tools including band saws and power drills. The concrete must be measured for compressive strengths, moisture content, bulk density, and shrinkage because it is lightweight and low-density.
In the manufacture of aircrete, the autoclave is usually a steel tube with a diameter of 3 meters and a length of 45 meters. Steam is pumped into the autoclave at a high pressure, usually 800 kPa and 180 °C. Several chemical reactions occur as AAC is mixed and cast in forms, giving it its light weight (20% of the weight of concrete) and thermal properties. Because of the low temperature, AAC blocks are classified as a lightweight concrete masonry device rather than a fired brick.
Walls, floors, roof panels, blocks, and lintels can all be made of autoclaved aerated concrete (AAC) concrete. Panels come in thicknesses ranging from 8 to 12 inches, widths of 24 inches, and lengths of up to 20 feet. The blocks are available in lengths of 24, 32, and 48 inches, as well as thicknesses ranging from 4 to 16 inches and a height of 8 inches.
Because of its low density, AAC has a low structural compression power. It has a compressive strength of up to 8 megapascals (1,200 psi), which is around half that of standard concrete. The first AAC material factory, the LCC SIPOREX – Lightweight Construction Company, opened in the Persian Gulf state of Saudi Arabia in 1978, supplying the GCC countries with aerated blocks and panels. Cured autoclaved aerated concrete blocks or panels are joined with thin bed mortar, using the same techniques as regular concrete blocks. Walls can be reinforced with steel or other structural members that run vertically through gaps in the blocks for added strength.
In both the way it is made and the composition of the finished product, autoclaved aerated concrete (AAC) differs from dense concrete (also known as “natural concrete”). There has been a worldwide growth in the use of AAC materials since 1980. Australia, Bahrain, China, Eastern Europe, India, and the United States are all constructing new manufacturing facilities. AAC is becoming more common among developers, architects, and home builders around the world. Because of its light weight, AAC concrete can be used for walls, floors, and roofs, making it more versatile than regular concrete. The material is solid and fire resistant, and it provides outstanding sound and thermal insulation. AAC must be coated with an applied finish, such as polymer-modified stucco, natural or engineered stone, or siding, in order to be durable.
Autoclaved aerated concrete, on the other hand, has a much lower density than dense concrete. The chemical reactions that form the hydration products are nearly complete during autoclaving, so the blocks are ready to use once removed from the autoclave and cooled. The outer face of AAC walls must be covered with a thick layer of waterproof material or membrane if used in basements. Surfaces of AAC that are exposed to the elements or soil moisture will deteriorate. There is no aggregate in it; all of the key mix materials, including milled sand, are reactive. Because of the high temperature and pressure in the autoclave, the sand, which is inert when used in dense concrete, behaves as a pozzolan.
AAC’s inherent insulation values are just mild, ranging from R-10 for an 8-inch-thick wall to R-12.5 for a 10-inch-thick wall. For each inch of material thickness, AAC has an R-value of about 1.25. Its manufacturing process varies slightly depending on the production plant, but the concepts are the same. AAC has a high thermal mass, which delays the transfer of thermal energy, lowering heating and cooling costs significantly. To minimize energy losses due to air leakage, the structures can be rendered extremely airtight. AAC also works well as a soundproofing shield.
Information Sources: