Precision arms for miniature robots typically consist of several components, including joints, links, actuators, and end effectors. The design of these components can vary depending on the specific requirements of the application.
One important consideration in the design of a precision arm for a miniature robot is the size and weight of the components. Miniature robots are often limited in terms of their size and weight capacity, so the arm must be designed to be as lightweight and compact as possible while still being strong enough to perform the required tasks.
Another important consideration is the precision and accuracy of the arm. This can be achieved through the use of high-quality materials and precision manufacturing processes. Additionally, the arm may be equipped with sensors or other feedback mechanisms to provide real-time feedback on its position and orientation.
Microscopic robotic systems have had to do without arms until now. Researchers have now created an ultrasonically actuated glass needle that can be connected to a robotic arm. This allows them to pump and mix minuscule amounts of liquid while also trapping particles. We are all familiar with robots that have moving arms. They can be programmed and stand in factory halls performing mechanical work. A single robot can perform a wide range of tasks.
Our work contributes to the convergence of the two approaches. As a result, future microfluidic systems could be designed in the same way that robotic systems are today. A single device that has been properly programmed could handle a variety of tasks.
Professor Daniel Ahmed
Miniature systems that transport tiny amounts of liquid through fine capillaries have had little association with such robots until now. Microfluidics or lab-on-a-chip systems were developed by researchers as a tool for laboratory analysis and typically use external pumps to move liquid through the chips. Such systems have been difficult to automate in the past, and the chips have had to be custom-designed and manufactured for each application.
Ultrasound needle oscillations
Traditional robotics and microfluidics are now being combined by scientists led by ETH Professor Daniel Ahmed. They created an ultrasound device that can be attached to a robotic arm. It is suitable for a wide range of tasks in microrobotic and microfluidic applications, as well as for automating such applications. The researchers published their findings in Nature Communications.
A thin, pointed glass needle and a piezoelectric transducer cause the needle to oscillate in the device. Transducers like these are found in loudspeakers, ultrasound imaging, and professional dental cleaning equipment. The ETH researchers can change the frequency of oscillation of their glass needle. They create a three-dimensional pattern of multiple vortices by dipping the needle into a liquid. Since this pattern depends on the oscillation frequency, it can be controlled accordingly.
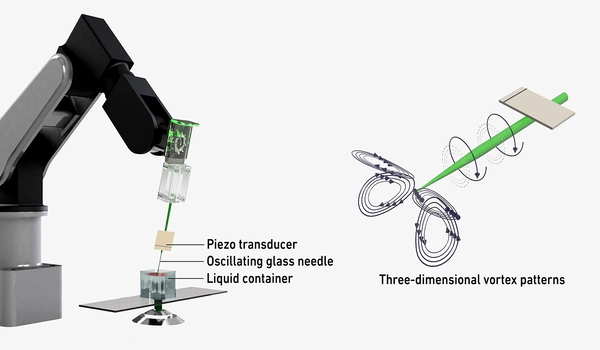
The researchers were able to use this to demonstrate several applications. First, they were able to mix tiny droplets of highly viscous liquids. “The more viscous liquids are, the more difficult it is to mix them,” Professor Ahmed explains. “However, our method succeeds in doing this because it allows us to not only create a single vortex, but to also efficiently mix the liquids using a complex three-dimensional pattern composed of multiple strong vortices.”
Second, the scientists were able to pump fluids through a mini-channel system by creating a specific pattern of vortices and placing the oscillating glass needle close to the channel wall.
Third, they were successful in trapping fine particles in the fluid using their robot-assisted acoustic device. This works because the size of a particle determines how it reacts to sound waves. Large particles gravitate toward the oscillating glass needle, where they accumulate. The researchers demonstrated that this method can capture both inanimate particles and fish embryos. They believe it should be able to capture biological cells in the fluid as well. “Manipulation of microscopic particles in three dimensions has always been difficult in the past. It’s simple with our microrobotic arm” Ahmed states.
“Up until now, advances in large, traditional robotics and microfluidic applications have been made separately,” Ahmed explains. “Our work contributes to the convergence of the two approaches.” As a result, future microfluidic systems could be designed in the same way that robotic systems are today. A single device that has been properly programmed could handle a variety of tasks. “We can mix liquids, pump them, and trap particles all with one device,” Ahmed says. This means that microfluidic chips of the future will no longer need to be custom-designed for each application. The researchers hope to combine several glass needles in the future to create even more complex vortex patterns in liquids.
Ahmed envisions other applications for microrobotic arms, such as sorting tiny objects, in addition to laboratory analysis. The arms could potentially be used in biotechnology to introduce DNA into individual cells. They should eventually be usable in additive manufacturing and 3D printing.