There are a number of techniques for performing underwater concreting, including the tremie method, pumping techniques, preplaced aggregate concrete, etc. Techniques for underwater concreting are primarily intended to stop cement washout. With the exception of situations when enormous quantities of concrete were used, these methods did not fully achieve the goal of preventing cement wash out at the beginning of employing under water concreting.
However, more modern methods might succeed in preventing concrete from washing out. In this article, various methods will be explored.
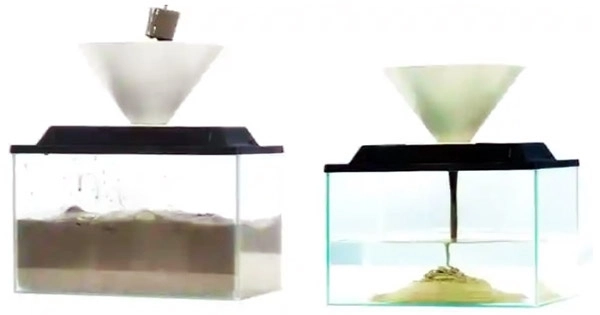
Methods of Underwater Concreting –
Following are the methods of underwater concreting:
- Tremie method
- Pumping technique
- Hydro valve method
- Pneumatic valve method
- Skip method
- Tilting pallet barge method
- Preplaced aggregate concrete
- Toggle bags method
- Bagged concrete method
Tremie Method of Underwater Concreting:
The tremie method for underwater concreting makes it simple to pour vast quantities of highly flowable concrete. Either pumping, a belt conveyer, or skips are used to transfer the concrete to the hopper. Concrete is placed at the precise spot from a hopper at the surface using a tremie pipe, which has its top end attached to a hopper and its bottom end continuously submerged in fresh concrete. To avoid mixing of both concrete and water, the bottom end of the tremie pipe should be submerged.
Process of Underwater Concreting using Tremie Method
There number of factors that should be considered during Tremie pipe technique of underwater concreting:
- Tremie Equipment – Tremie pipes can be set up in three distinct methods, including telescope pipes, pipes with different parts that are disassembled after concreting, and pipes of a constant length that are raised. Because of the chemical reactions that can occur between an aluminum alloy pipe and the concrete, it should be avoided. The pipe should have an adequate diameter to prevent blockage because of aggregate size. The usual diameter is between 200- 300 mm and occasionally 150 mm and 450 mm could be used but aggregate size should be considered for example 19 mm and 40 mm aggregate size is lower limit for 150 mm 200 mm pipe diameter respectively.
- Tremie seal – A wooden plat plug is used to seal the pipe’s end to prevent water and concrete from mixing inside the pipe. This keeps the pipe dry and stops water from entering it. Concrete is poured to break the seal when the pipe has reached its target location. Then concrete flows out of the pipe and builds up around the pipe’s lower end, sealing it off.
- Placing the concrete – As soon as concreting began the pipe mouth should be submerged up to 1- 1.5 m into fresh concrete to prevent water entering the pipe. Concrete flow rate is controlled by lowering and rising the pipe, and either a drop or a rise in concrete discharge signals a broken seal, therefore concrete flow should be continuous and closely observed.
- Flow pattern – Two types of flow pattern are recognized namely, layered and bulging. The homogeneous displacement of the concrete caused by the bulging flow is preferred since it results in less laitance deformation and flatter slopes.
Underwater Concreting using Pumping Technique:
A more advanced variant of Tremie pipe, underwater concreting employing pumping technique offers a quicker way to pour concrete in hard-to-reach places, like underneath piers. Pumping has various benefits that Tremie pipe does not, such as the direct pouring of concrete from the mixer to the formwork, the removal of obstructions in the pipe due to the use of pumping rather than gravity force, and a reduced chance of segregation.
Hydro Valve Method of Underwater Concreting:
This method of underwater concreting is developed and employed by the Dutch in 1969. A flexible hose which hydrostatically compressed is employed to pour concrete. As soon as concrete is poured into the pipe’s upper section, the weight of the concrete overcomes both internal pipe friction and hydrostatic pressure. In order to prevent segregation, the concrete is moved slowly through the pipe. A rigid tubular section is used to seal the end of the hose. This method is not costly and quite simple.
Underwater Concreting using Pneumatic Valves:
Pneumatic valves are joined to the end of the pipe line of concrete. Different valve types, including Abetong-Sabema and Shimizu, are used for underwater concreting. These two valves are similar, with the exception of the sensor attached to the latter, whose purpose is to close the valve when the thickness of the concrete reaches a predetermined level. There is another form of valve that can be used to pour concrete at a depth of 52 meters without submerging the pipe’s end. The function of the valves is to permit, restrict, stop the discharge of concrete and this method is the useful technique.
Underwater Concreting using the Skips Method:
A bucket with two bottom-opening doors and overlapping canvas flaps that are installed at the top to prevent concrete washing is used to transport concrete. Once the skip is full of concrete, it is slowly dropped through water to its destination, where the doors are either automatically or manually opened. When a huge mass of concrete is needed to stabilize foundations and smaller amounts are needed at various locations, the Skip technique of underwater concreting is appropriate.
Underwater Concreting using Tilting Pallet Barge:
This technique is useful for shallow water and the concrete is poured in thin layers. A tilting pallet is built along the barge’s deck, where concrete is spread evenly and then allowed to fall freely into the water.
Underwater Concreting using Preplaced Aggregate Concrete:
Preplaced aggregate concrete is an excellent option when laying regular concrete would be challenging or unlikely. It involves filling the forms with aggregate, injecting concrete into the bottom, and then filling the forms all the way up. Concreting is starting at the bottom to avoid trapping water and air. For this reason, the tubes must be placed in the forms before the aggregate. Concrete strength about 70 to 100 percent of conventional concrete can be obtained in this technique. The pipes are distributed with the maximum distance of 1.5 m and their diameters ranges from 19 – 35 mm.
Toggle Bags Method:
Toggle Bags method is useful when small amount of concrete is required. Concrete is carefully dropped into a reusable canvas bag that is closed at the top with a chain and fastened with toggles. The concrete is then released via an aperture at the bottom of the bag.
Bagged Concrete Method:
Bagged concrete method used for renew ballast or to seal holes temporarily. The bags, which have a capacity of 10 to 20 liters and are made of a remarkably sturdy fabric, are transported to the desired location by divers. The greatest aggregate size that may be used is 40 mm, and the concrete slump ranges from 19 to 50 mm. The installation of the bags is similar to bricks in order to create bonds.