Several factors, such as steel corrosion in an aggressive environment, design calculation errors, and poor mix design, could lower the ultimate load capacity of concrete structures. One such factor is the use of near surface mounted fiber reinforced polymer bars for strengthening of reinforced concrete beams. It is not cost-effective to demolish deteriorating structures and rebuild them.
Therefore, it is crucial to improve and strengthen the peak performance or regain strength of damaged structures. Improvements to reinforced concrete components have been made using a variety of methods and techniques, including externally bonded plates, which used steel plate, and FRP layers. One of the many techniques used to enhance reinforced concrete components is the near surface mounted fiber reinforced polymer technology.
Near Surface Mounted FRP Technique Procedures:
- Cutting grooves on the cover of the beam along tension side.
- Use brushes and pressurized air to remove debris in the grooves.
- Epoxy past or grout cement is inserted in to 2/3 of the groove as binder.
- FRP bar is pushed into the binder materials until it encircled by the binder agent.
- Finally, the remaining part of the groove is filled with the epoxy paste.
Steel reinforcements should not be cut during this process or the element will lose all of its capacity. Therefore, in order to be strengthened using this method, a reinforced concrete element must have a minimum 20 mm cover.
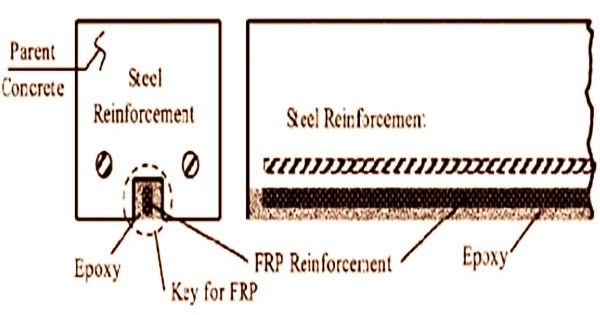
Properties of FRP bars:
There are three types of FRP bars namely, Carbon, Aramid, Glass FRP bars. As shown in figure 2 tensile strength of FRP bars are more than steel reinforcement and lacking yield point is a clear distinction of FRP bars. FRP bars are corrosion resistant which is a substantial advantage over steel. Due to high tensile strength FRP bars can resist larger loads.
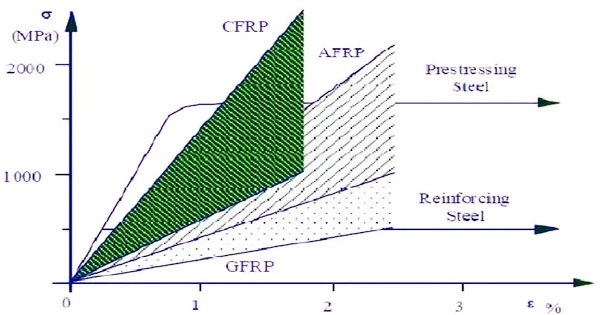
Advantages of Near Surface Mounted Fiber Reinforced Polymers Technique:
- This method can be handled easily in the field due to the weight of FRP bars.
- It is not prone to corrosion in hostile environment.
- Due to the concrete and binder agent covering the FRP bars, they are shielded from damaging mechanical impact.
- After the elements have been strengthened, their structural appearance has hardly changed.
Disadvantages of NSM FRP Technique:
- There are no approved codes to use as guidance.
- FRP bars are expensive compared with steels.
- FRP bars have low transverse strength and it can be damaged by fire or vandalism.
Design of Near Surface Mounted Fiber Reinforced Polymers Technique:
Since no formal design code exists, a variety of models have been created to predict the failure of strengthened elements and estimate their maximum capacity. It is very crucial to conduct inspection and collect data about deteriorated beams such as:
Main reinforcement ratio, if the element is over reinforced, strengthening will be less effective because, as applied load increases, the beam may fail in compression, which is not permitted by ACI Code. Reinforcement ratio can be obtained from previous design calculations.
To determine whether adopting this technique is practical, the thickness of the concrete cover should be determined. If a design calculation is not available, the concrete cover can be determined using a magnetic rebar finder (cover meter) test or by removing a small portion of the concrete to reveal the primary reinforcement.
Factors affecting design of NSM Fiber Reinforced Polymer Concrete:
There are several parameters which affect the design:
- Spacing between grooves.
- Concrete thickness between FRP and steel bars.
- Concrete compressive strength.
- Axial rigidity of fiber reinforced polymer bars
- NSM FRP bars to groove perimeter.
- FRP to steel reinforcement ratio.
- The effect of the distance between beam edge and grooves.
Types of failure in strengthened reinforced concrete beams
There are two major failures:
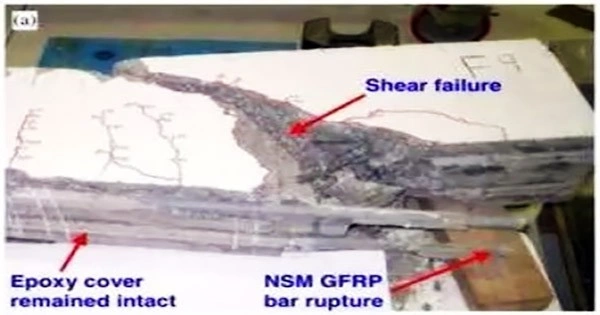
Rupture of FRP bars followed by crushing of concrete: this types of failure occurs when the bond between concrete and FRP is strong.
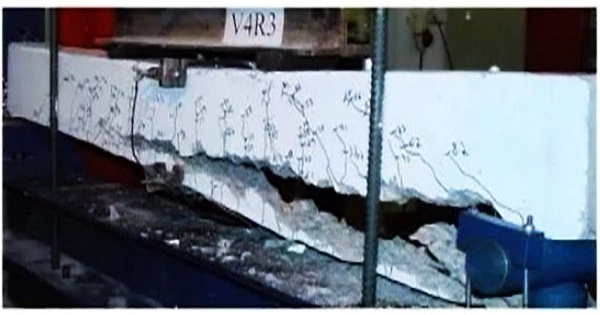
Premature failure: this type of failure happens when the bond between FRP bars and concrete is broken, and it can take many different shapes and manifest through a variety of mechanisms, including splitting of the concrete cover, failure at the interface between concrete and epoxy, and failure at the interface between the bars and epoxy.