With the widespread usage of single-use masks during the pandemic now posing an environmental risk, researchers have proven the idea of integrating used masks into a cement mixture to make stronger, more lasting concrete.
According to a news release from Washington State University, researchers utilized disposable masks to boost the strength of concrete by up to 47 percent. As the coronavirus pandemic continues, so does the use of disposable masks, which frequently end up littering not only public spaces but also our waters. A research published last year predicted that mask pollution increased by 9,000 percent when countries adopted mask mandates to control the spread of the illness. However, the billions of masks produced during this period have become a massive challenge for waste management.
A Washington State University research team demonstrated in a report published in the journal Materials Letters that the combination containing mask materials was 47 percent stronger than routinely used cement after a month of curing.
“These waste masks could actually be a lucrative product if properly processed,” said Xianming Shi, professor and interim chair of the Department of Civil and Environmental Engineering and the paper’s corresponding author. “I’m always on the lookout for waste streams, and my first thought is, ‘How can I turn that into something usable in concrete or asphalt?'”
These waste masks could actually be a lucrative product if properly processed. I’m always on the lookout for waste streams, and my first thought is, ‘How can I turn that into something usable in concrete or asphalt?’
Professor Xianming Shi
Cement production is a carbon-intensive process that accounts for up to 8% of global carbon emissions. Microfibers are already used to strengthen cement concrete, but they are pricey. Microfiber-reinforced concrete has the potential to lower the quantity of cement required for a project or to extend the life of the concrete, saving carbon emissions as well as money for builders and owners.
Medical masks have fibers that can be useful in the concrete industry since they are made of a polypropylene or polyester fabric where it contacts the skin and an ultra-fine polypropylene fiber for the filtering layers. Disposable masks can linger in the environment for decades if not reused, posing a harm to the ecosystem.
“This work showcases one technology to divert the used masks from the waste stream to a high-value application,” Shi said.
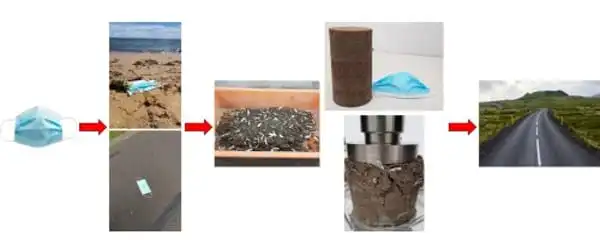
In their proof-of-concept study, the researchers created a method for fabricating microscopic mask fibers ranging from five to thirty millimeters in length, which they then placed to cement concrete to strengthen and prevent cracking. They removed the metal and cotton loops from the masks, chopped them up, and integrated them into ordinary Portland cement, the most common type of cement used throughout the world and the primary ingredient for concrete, mortar, and grout.
They put the mask microfibers into a graphene oxide solution before adding the mixture to cement paste. The graphene oxide creates ultrathin coatings that tightly attach to the fiber surfaces. Such mask microfibers absorb or dissipate the fracture energy that would contribute to tiny cracks in the concrete. Without the fibers, these microscopic cracks would eventually lead to wider cracks and the material’s failure.
More study is being conducted to evaluate the researchers’ hypothesis that graphene oxide-treated microfibers could improve concrete durability and protect it from frost damage and deicing chemicals used on roadways. They also intend to apply this method to the recycling of other polymer materials, such as abandoned garments, in order to promote the collecting of such garbage.
Used face masks from the COVID-19 epidemic are creating a new waste stream that, if not properly disposed of, poses a significant environmental risk to the ecosystem. This study looked into an environmentally friendly way to convert such waste to a value-added application, namely the fabrication of waste mask microfibers for use in cementitious composites. Microfibers manufactured from recycled medical masks are pre-treated in an aqueous solution of graphene oxide to increase the interfacial transition zone between mask fibers and cement paste matrix (GO, at 0.05 wt percent).