The School of Biosciences at the University of Kent has designed and manufactured equipment that can be used to research bacterial biofuel generation at a quarter of the cost of commercial systems. This approach was then utilized to show how bacterial genetic engineering could be applied to improve biofuel production.
A bioreactor is a device used to cultivate organisms (such as yeast, bacteria, or animal cells) under regulated circumstances. It is used in the manufacturing of medicines, vaccines, and antibodies. It is also used to transform basic materials into valuable byproducts, such as corn bioconversion to ethanol.
Commercial equipment used to investigate biofuel-producing bacteria can be prohibitively expensive, so the team decided to create their own bioreactors, which are available to most research institutes. The researchers then utilized this technology to confirm that one of their genetically altered Clostridium bacterium strains could generate butanol more quickly.
These exciting developments will help to advance research into bacterial biofuel production, and we are especially excited to use our expertise to optimize processes that can convert waste products from food and agriculture into biofuels that are greener alternatives to fossil fuels.
Dr. Mark Shepherd
The heart of biological processes is the bioreactor. Extensive studies on the biological system, such as cell growth, metabolism, genetic manipulation, and protein or other product expressions, are required to understand the cells’ requirements on their physical and chemical environments in order to design an appropriate bioreactor system for a specific bioprocess. In order to favor the intended functions of cells and accomplish cost-effective large-scale manufacturing, the bioreactor environment must also be controlled and optimized using operating variables.
These findings, published in the journals Access Microbiology and Microbial Biotechnology, show that a little mutation in a single gene can result in dramatic changes in how carbohydrates are transformed into biofuel products. This approach is likely to provide access to less expensive bioreactors, thus stimulating more research into biofuel generation utilizing natural and artificial bacteria.
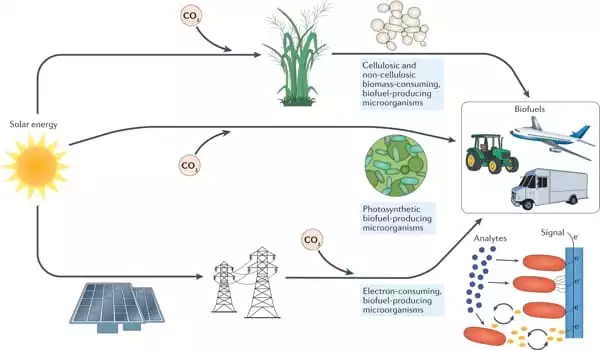
‘These exciting developments will help to advance research into bacterial biofuel production, and we are especially excited to use our expertise to optimize processes that can convert waste products from food and agriculture into biofuels that are greener alternatives to fossil fuels,’ said Dr. Mark Shepherd, Senior Lecturer in Microbial Chemistry at Kent.
The heart of biological processes is the bioreactor. Extensive studies on the biological system, such as cell growth, metabolism, genetic manipulation, and protein or another product expression, are required to understand the cells’ requirements on their physical and chemical environments in order to design an appropriate bioreactor system for a specific bioprocess. In order to favor the intended functions of cells and accomplish cost-effective large-scale manufacturing, the bioreactor environment must also be controlled and optimized using operating variables.
Microbial pollution treatment entails using microbes to degrade pollutants, either totally to water and carbon dioxide (for organic pollutants) or into less hazardous forms. Bioremediation of nonbiodegradable inorganic chemicals takes the form of bioaccumulation or conversion of one hazardous species to a less toxic one, for example, Cr(VI) is changed to a less toxic form (III).
Bioremediation is regarded as an environmentally beneficial method of pollution cleanup. Microbial cleaning can be done in situ (at the location of contamination) or ex situ (off the site of contamination). In situ remediation in the natural environment is thought to be slow and difficult to control and optimize the various parameters affecting bioremediation.