Silicon nitride (Si3N4) is a chemical compound composed of silicon and nitrogen. It is a non-oxide structural ceramic material that is typically black or dark grey in color and is frequently polished to provide a smooth and highly reflective surface appearance. It has the highest thermodynamic stability of silicon nitrides. Its typical applications include metal forming, industrial wear situations, and molten metal handling, and it is well known for its high shock and thermal resistance.
As a result, when the term “silicon nitride” is used, Si3N4 is the most commercially important of the silicon nitrides. It is a white, high-melting-point solid that is relatively chemically inert, with dilute HF and hot H2SO4 attacking it. It is extremely difficult (8.5 on the Mohs scale). It has excellent thermal stability.
Key Properties:
- low density
- high temperature strength
- superior thermal shock resistance
- excellent wear resistance
- good fracture toughness
- mechanical fatigue and creep resistance
- good oxidation resistance
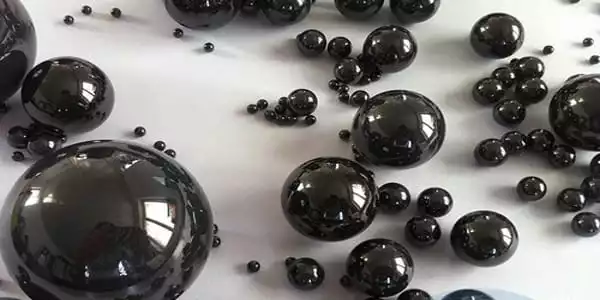
Production
Silicon nitride is typically created through the chemical reaction of metallic silicon and gaseous nitrogen. Parts are carefully pressed and sintered using well-developed methods, which result in specific properties and, as a result, define the end applications.
The material will be prepared by heating powdered silicon between 1300 °C and 1400 °C in a nitrogen environment:
3 Si + 2 N2 → Si3N4
The chemical combination of silicon and nitrogen causes the weight of the silicon sample to gradually increase. When no further weight increase due to nitrogen absorption (per gram of silicon) is detected after several hours in the absence of an iron catalyst, the reaction is complete. In addition to Si3N4, several other stoichiometric silicon nitride phases (with chemical formulas corresponding to varying degrees of nitridation/Si oxidation state) have been reported in the literature, including gaseous disilicon mononitride (Si2N), silicon mononitride (SiN), and silicon sesquinitride (Si2N3).
The products obtained in these high-temperature syntheses, like those obtained in other refractories, are dependent on the reaction conditions (e.g., time, temperature, and starting materials, including the reactants and container materials), as well as the mode of purification. However, the sesquinitride’s existence has since been called into question.
It can also be prepared by diimide route:
SiCl4 + 6 NH3 → Si(NH)2 + 4 NH4Cl(s); at 0°C
3 Si(NH)2 → Si3N4 + N2 + 3 H2(g); at 1000°C
Carbothermal reduction of silicon dioxide in a nitrogen atmosphere at 1400–1450°C has also been examined:
3 SiO2 + 6 C + 2 N2 → Si3N4 + 6 CO
Following the “rediscovery” of silicon nitride in the 1950s, the nitridation of silicon powder was developed as the first large-scale method for powder production. However, the use of low-purity raw silicon resulted in silicate and iron contamination of silicon nitride. The diimide decomposition produces amorphous silicon nitride, which requires additional annealing under nitrogen at 1400–1500°C to convert to crystalline powder; this is now the second-most important commercial production route. The carbothermal reduction was the first method used to produce silicon nitride and is now regarded as the most cost-effective industrial route to high-purity silicon nitride powder.
Applications
Silicon nitride produces high-quality components for use in extremely demanding applications due to its ability to withstand the rigors of severe thermal, mechanical, and wear situations.
The automobile industry – The automotive industry uses silicon nitride the most, particularly in various wear and combustion parts in reciprocating engines where high-temperature stresses are common.
Bearings – For high-temperature applications, silicon nitride ceramic ball and roller bearings are preferred over steel. This increases bearing life at higher speeds because it is more corrosion resistant.
Metalworking – Due to its hardness, fracture toughness, and thermal shock resistance, silicon nitride is also used in metal cutting tools for cast iron, hard steel, and nickel-based alloys.