Microchip sensors are essential components in a wide range of electronic devices, including smartphones and medical devices. Materials with specific properties, such as electrical conductivity, thermal stability, and mechanical strength, are frequently used in these sensors. Silicon, silicon carbide, and various polymers are common materials used in microchip sensors.
Amorphous silicon carbide (a-SiC), discovered by Delft University of Technology researchers led by assistant professor Richard Norte, has the potential to change the world of material science. Aside from its exceptional strength, this material has mechanical properties that are critical for vibration isolation on a microchip. As a result, amorphous silicon carbide is particularly well suited to the fabrication of ultra-sensitive microchip sensors.
The range of potential applications is vast. From ultra-sensitive microchip sensors and advanced solar cells to pioneering space exploration and DNA sequencing technologies. The advantages of this material’s strength combined with its scalability make it exceptionally promising.
To grasp what this means, imagine trying to stretch a piece of duct tape until it breaks. Now if you’d want to simulate the tensile stress equivalent to 10 GPa, you’d need to hang about ten medium-sized cars end-to-end off that strip before it breaks.
Richard Norte
Ten medium-sized cars
“To better understand the crucial characteristic of “amorphous,” think of most materials as being made up of atoms arranged in a regular pattern, like an intricately built Lego tower,” explains Norte. “These are known as “crystalline” materials, such as diamonds. It has perfectly aligned carbon atoms, which contributes to its famed hardness.” Amorphous materials, on the other hand, are like a randomly piled set of Legos, with atoms that lack consistent arrangement. However, contrary to popular belief, randomization does not result in fragility. In fact, amorphous silicon carbide is proof that strength can emerge from such randomness.
The tensile strength of this new material is 10 GigaPascal (GPa). “To grasp what this means, imagine trying to stretch a piece of duct tape until it breaks. Now if you’d want to simulate the tensile stress equivalent to 10 GPa, you’d need to hang about ten medium-sized cars end-to-end off that strip before it breaks,” says Norte.
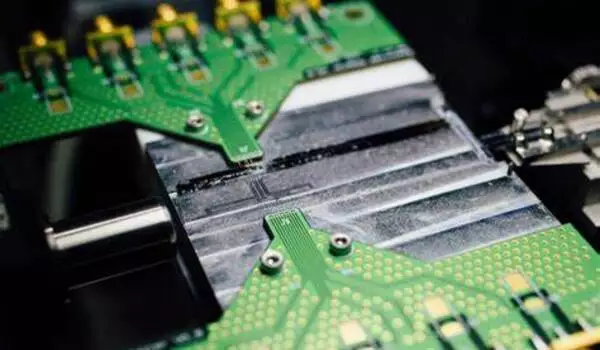
Nanostrings
The researchers used an innovative method to test the tensile strength of this material. They used microchip technology instead of traditional methods, which could introduce inaccuracies due to the way the material is anchored. They used the geometry of the nanostrings to induce high tensile forces by growing amorphous silicon carbide films on a silicon substrate and suspending them. They meticulously observed the point of breakage by fabricating many such structures with increasing tensile forces. This microchip-based approach ensures unprecedented precision while also paving the way for future material testing.
Why the focus on nanostrings? “Nanostrings are fundamental building blocks, the very foundation that can be used to construct more intricate suspended structures. Demonstrating high yield strength in a nanostring translates to showcasing strength in its most elemental form.”
From micro to macro
Finally, the scalability of this material distinguishes it. Graphene, a single layer of carbon atoms, is known for its incredible strength but is difficult to mass produce. Diamonds, despite their immense strength, are either rare in nature or expensive to synthesize. Amorphous silicon carbide, on the other hand, can be manufactured at wafer scales, resulting in large sheets of this extremely robust material.
“With amorphous silicon carbide’s emergence, we’re poised at the threshold of microchip research brimming with technological possibilities,” says Norte.