Plastic can be ‘synthetic’ or ‘biobased.’ The raw materials for synthetic plastics are crude oil, natural gas, or coal. Biobased plastics, on the other hand, are made from renewable materials such as carbohydrates, starch, vegetable fats and oils, bacteria, and other biological substances. Because of the ease of manufacturing methods involved in crude oil processing, the vast majority of plastic in use today is synthetic. However, the growing demand for limited oil reserves is driving a demand for newer plastics made from renewable resources such as waste biomass or industrial animal waste.
Scientists have created a new PET-like plastic that can be easily made from non-edible plant parts. Because the plastic is tough, heat-resistant, and a good barrier to gases such as oxygen, it is a promising candidate for food packaging. Because of its structure, the new plastic can also be chemically recycled and degraded in the environment to harmless sugars.
EPFL researchers have created a new PET-like plastic that can be easily made from non-edible plant parts. Because the plastic is tough, heat-resistant, and a good barrier to gases such as oxygen, it is a promising candidate for food packaging. Because of its structure, the new plastic can also be chemically recycled and degraded in the environment to harmless sugars.
By using a different aldehyde – glyoxylic acid instead of formaldehyde – we could simply clip ‘sticky’ groups onto both sides of the sugar molecules, allowing them to act as plastic building blocks. We can convert up to 25% of the weight of agricultural waste or 95% of purified sugar into plastic using this simple technique.
Lorenz Manker
It is becoming increasingly clear that shifting away from fossil fuels and avoiding the accumulation of plastics in the environment are critical to addressing the challenge of climate change. In that vein, significant efforts are being made to develop degradable or recyclable polymers derived from non-edible plant material known as “lignocellulosic biomass.”
Of course, producing competitive biomass-based plastics is not easy. There’s a reason why conventional plastics are so popular: they combine low cost, heat stability, mechanical strength, processability, and compatibility – characteristics that any alternative plastic replacement must match or exceed. And so far, the task has been difficult.
That is, until now. Scientists at EPFL’s School of Basic Sciences, led by Professor Jeremy Luterbacher, have successfully developed a biomass-derived plastic, similar to PET, that meets the criteria for replacing several current plastics while also being more environmentally friendly.
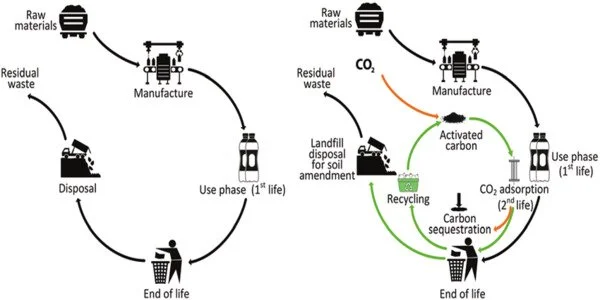
“We essentially just ‘cook’ wood or other non-edible plant material, such as agricultural wastes, in inexpensive chemicals to produce the plastic precursor in a single step,” Luterbacher explains. “The chemistry is much simpler than current alternatives because the sugar structure is kept intact within the molecular structure of the plastic.”
The method is based on a 2016 discovery made by Luterbacher and his colleagues, who discovered that adding an aldehyde could stabilize certain fractions of plant material and prevent them from being destroyed during extraction. The researchers were able to create a new useful bio-based chemical as a plastic precursor by repurposing this chemistry.
“By using a different aldehyde – glyoxylic acid instead of formaldehyde – we could simply clip ‘sticky’ groups onto both sides of the sugar molecules, allowing them to act as plastic building blocks,” says the study’s first author, Lorenz Manker. “We can convert up to 25% of the weight of agricultural waste or 95% of purified sugar into plastic using this simple technique.”
These plastics’ well-rounded properties may enable them to be used in applications ranging from packaging and textiles to medicine and electronics. The researchers have already created packaging films, fibers that could be spun into clothing or other textiles, and filaments for 3D printing.
“The plastic has very exciting properties, particularly for applications such as food packaging,” says Luterbacher. “The presence of the intact sugar structure distinguishes the plastic. This makes it incredibly simple to make because you don’t have to modify what nature provides, and simple to degrade because it can degrade back to a molecule that is already abundant in nature.”