In a study published in Nano Letters, physicists provided an unexpected boost for researchers by developing a new technique for 3D nanoscale elemental analysis for ion-electron microscope systems, allowing the scientific community to take their work to the next level, particularly in the fields of energy storage and sustainability.
Thermo Fisher Scientific scientists collaborated with the ARC Centre of Excellence for Transformative Meta-Optical Systems (TMOS) to develop a device that can be retrofitted to existing focused ion beam systems (FIBS). This device reimagines how the FIB is used, transforming it from a sputtering tool to an engine for elemental characterization, collecting and analyzing photons emitted during the sputtering process.
This new method offers a number of improvements to other characterization methods. In particular, it offers a resolution of 15 nanometers, a significant improvement on the 1-micron resolution of electron-based EDX technique. Additionally, it can detect hard-to-characterize elements such as hydrogen and lithium.
This research was geared toward enabling other researchers to solve problems in an efficient way. Integrating elemental analysis as part of the sputtering process optimizes the characterization workflow, creating a better experience for all involved. We’ve developed this new technique so others can develop new technologies in a range of fields.
John Scott
Lead author and Senior Scientist at Thermo Fisher Scientific Garrett Budnik says, “the characterization of light elements has always been a challenge. This new device fills what was previously a gap in technology, paving the way for further scientific advancement.
“When that happens and researchers can investigate their problems with new techniques, new discoveries are made.”
University of Technology Sydney (UTS) post-doctoral researcher and co-author John Scott says, “This research was geared toward enabling other researchers to solve problems in an efficient way. Integrating elemental analysis as part of the sputtering process optimizes the characterization workflow, creating a better experience for all involved. We’ve developed this new technique so others can develop new technologies in a range of fields.”
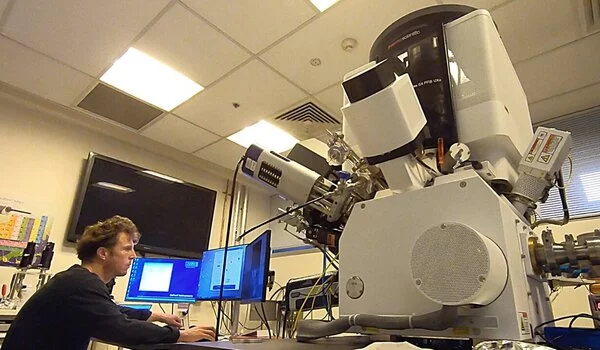
Budnik is the third Thermo Fisher Scientific employee to engage with the university in an industry-relevant Ph.D., working on projects designed by Thermo Fisher Scientific based on their deep understanding of gaps in the commercial market and industry-leading technology development.
TMOS Chief Investigator Milos Toth, who worked at Thermo Fisher Scientific as a research scientist before joining UTS as a professor, says, “Shared research between industry and academia are successful because they result in commercially-driven research. On their own, academic researchers might invest their energy in research that has little market appeal. Industry might develop rigorously-tested technology without fully understanding the fundamental science behind it. Together, they can make a significant contribution to society.”
Scott states, “We could only conduct this research because we had access to Thermo Fisher’s engineers. Our FIB is probably the most heavily modified microscope in the world, and that’s because we had access to the people who designed it, people who could help us tear it apart and reassemble it.”
Budnik says, when discussing the future of their research, “We’ve taken this detection system to its logical conclusion. It has been optimized to the point where the only way forward is to use metasurfaces. That is the logical next step.”