Crop-based bioenergy is a long-term alternative to fossil fuels. Energycane, a new crop, may yield three times the amount of fuel per acre as soybeans. However, processing the crops to extract fuel effectively remains a difficulty. Chemical-free pretreatment approaches, the development of high-throughput phenotyping tools, and the commercial-scale techno-economic feasibility of generating fuel from energycane in various scenarios are all explored in four new research from the University of Illinois.
The research is part of the University of Iowa’s ROGUE (Renewable Oil Generated with Ultra-Productive Energycane) initiative. ROGUE focuses on bioengineering the buildup of triacylglycerides (TAGs) in energycane leaves and stems, allowing for significantly higher yields of industrial vegetable oil per acre than previously feasible.
“The productivity of these non-food crops is very high per unit of land. Soybean is the traditional crop used for biodiesel, but we can get higher yield, more oil, and subsequently more biofuel from lipid-producing energycane,” says Vijay Singh, Founder professor in the Department of Agricultural and Biological Engineering (ABE) at U of I and co-author on all four papers.
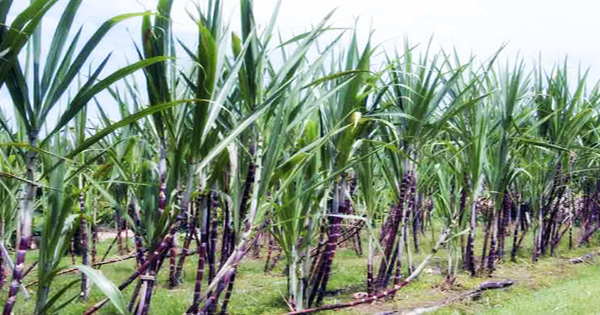
According to study co-author Deepak Kumar, assistant professor in the Chemical Engineering Department at State University of New York College of Environmental Science and Forestry (SUNY-ESF) and adjunct research scientist at the Carl R. Woese Institute for Genomic Biology at the University of Illinois, biofuel production from crops entails breaking down the cellulosic material and extracting the oil in a series of steps.
“The first step is to extract the juice. That leaves bagasse, a lignocellulosic material you can process to produce sugars and subsequently ferment to bioethanol,” Kumar says.
“One of the critical things in processing any lignocellulosic biomass is a pretreatment step. You need to break the recalcitrant structure of the material, so enzymes can access the cellulose,” he adds. “Because energycane is a novel crop, there are limited research on pretreatment and breakdown of the bagasse to create sugars and convert those sugars to biofuels.”
Unwanted chemicals are produced during the pretreatment process, which block enzymes that convert sugar to biofuels. The University of Illinois researchers looked at the optimal pretreatment techniques for maximizing breakdown while reducing inhibitor development. Chemicals like as sulfuric acid are typically used in the pretreatment process to break down the biomass at high temperatures and pressures.
“We use a chemical-free method, which makes it more environmentally friendly,” Kumar explains. “Furthermore, harsh chemicals may alter the oil structure or quality in the biomass.”
The researchers put their approach to the test with nine different temperature and time interval combinations. At the ideal circumstances, they were able to convert more than 90% of the cellulose, which is comparable to the results of chemical pretreatment techniques. The second research drew on previous findings to look at the link between temperature, inhibitor production, and sugar recovery in greater depth.
“We pretreated the lignocellulosic biomass over a range of different temperatures to optimize the condition for minimal inhibitor generation without affecting the sugar recovery. Then we added cryogenic grinding to the process,” says Shraddha Maitra, postdoctoral research associate in ABE and lead author on the study.
“In cryogenic grinding, you treat the bagasse with liquid nitrogen, which makes it very brittle, so upon grinding the biomass fractures easily to release the sugars. This further increased sugar recovery, mainly xylose, by about 10% compared to other refining processes,” Maitra explains.
Similar processes are used in other sectors, such as spices and essential oils, when it is crucial to maintain the product’s characteristics. However, putting them to use in the manufacture of biofuels is a novel concept.
In third research, Maitra and her co-authors used time-domain nuclear magnetic resonance (NMR) technology to monitor changes in total, bound, and free lipids following various physical and chemical feedstock preparation methods to assess the stability and recovery of lipids.
The fourth study conducted by the research team looked at the commercial-scale techno-economic feasibility of an engineered energycane-based biorefinery. In comparison to soybean-based biodiesel, they utilized computer modeling to simulate the manufacturing process under two distinct scenarios to estimate capital investment, production costs, and output.
“Although the capital investment is higher compared to soybean biodiesel, production costs are lower (66 to 90 cents per liter) than for soybean (91 cents per liter). For the first scenario, processing energycane had overall slightly lower profitability than soybean biodiesel, but yields five times as much biodiesel per unit of land,” says Kumar, the lead author on the study.
“Energycane is attractive in its ability to grow across a much wider geography of the U.S. south east than sugarcane. This is a region with much underutilized land, yet capable of rain-fed agriculture,” says ROGUE Director Steve Long, Ikenberry Endowed Chair of Plant Biology and Crop Sciences at the University of Illinois.
“As a perennial, energycane is suitable for land that might be damaged by annual crop cultivation. Our research shows the potential to produce a remarkable 7.5 barrels of diesel per acre of land annually. Together with co-products, this would be considerably more profitable than most current land use, while having the potential to contribute greatly to the national U.S. goal of achieving net-zero greenhouse gas emissions by 2050. This proves how valuable it is to build on the successes already achieved in bioengineering energycane to accumulate oils that are easily converted into biodiesel and biojet,” Long states.