A metal foam is a cellular structure made of a solid metal (typically aluminum) with gas-filled pores that make up a large portion of the volume. Metal foams have a large number of nonconductive pores and have a lower electrical conductivity than the corresponding base materials. The pores can be sealed (closed-cell foam) or interconnected (open-cell foam) (open-cell foam). Metal foams are distinguished by their high porosity: the base metal accounts for only 5–25 percent of the volume. The square-cube law is responsible for the material’s strength.
Metal foams typically retain some of their base material’s physical properties. The non-flammable metal foam remains non-flammable and, in most cases, can be recycled as the base material. It has a similar coefficient of thermal expansion, but its thermal conductivity is likely reduced. This is a very specific application of metal/particle composites because the particles’ primary function is to modify the properties of a metallic melt and allow it to be processed into a metal foam.
Metal foams are made by forming a large number of gas-filled bubbles in a metallic melt and allowing them to agglomerate before the liquid is solidified into a solid foam. There are various methods for creating such foams, which vary depending on the type of gas used, the state of metal used (solid or liquid), how the bubbles are stabilized, and the procedures used. Aside from the standard aluminum alloys, a variety of metals and alloys can be processed into foams.
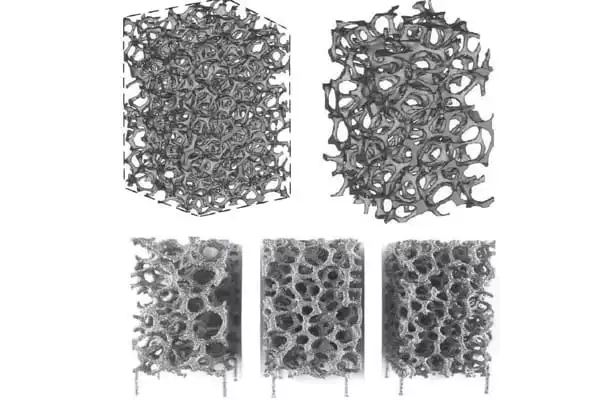
Properties of Metal Foam
The key properties of the metal foam are as follows:
- Ultralight material (75–95% of the volume consists of void spaces),
- Very high porosity,
- High compression strengths combined with good energy absorption characteristics,
- Thermal conductivity is low,
- High strength.
Metal foam is a cellular structure composed of solid metal with gas-filled pores that contain a high volume fraction. Metal foams are classified into two types: closed-cell foam and open-cell foam, depending on whether the pores are sealed or interconnected.
Heat exchangers (compact electronics cooling, cryogen tanks, PCM heat exchangers), energy absorption, flow diffusion, and lightweight optics can all benefit from open-celled metal foam, also known as a metal sponge. The material’s high cost generally limits its use to advanced technology, aerospace, and manufacturing.
Meller first reported closed-cell metal foam in a French patent in 1926, where foaming of light metals, either by inert gas injection or by blowing agent, was suggested. Benjamin Sosnik, who used mercury vapor to blow liquid aluminum, received two patents on sponge-like metal in 1948 and 1951. The majority of metal foams used in industry and research are made of aluminum, nickel, or titanium; however, a growing number of metallic systems have been produced and characterized.