Plastic separation anxiety can be defined as a reluctance or difficulty in separating oneself from the convenience of plastic in everyday life. Bio-based plastics, such as polylactic acid (PLA), were developed to aid in the resolution of the plastic waste crisis, but they frequently make waste management more difficult. Because these materials resemble traditional, petroleum-based plastics in appearance and feel, many products end up in the recycling stream rather than composters, where they degrade as intended.
The products are shredded and melted with recyclable plastics, lowering the quality of the mixture and making it more difficult to manufacture functional products from recycled plastic resin. Currently, the only solution is to try to separate the various plastics at recycling facilities. Even with the most sophisticated, automated sorting equipment, some biobased plastics contaminate the sorted streams.
Scientists at Lawrence Berkeley National Laboratory (Berkeley Lab) and the Joint BioEnergy Institute (JBEI) are collaborating with X, Alphabet’s parent company’s moonshot incubator, to not only avoid the problematic separation step, but also to make the final product better for the environment.
Chemical recycling has been a hot topic, but it’s difficult to make it happen on a commercial scale because all the separation steps are so expensive. However, by using a biocompatible catalyst in water, microbes can directly convert the depolymerized plastics without the need for additional separation steps.
Ning Sun
Using naturally derived salt solutions and specialized microbes, the team devised a simple “one pot” process for breaking down mixtures of petroleum-based and bio-based plastics. The salts act as a catalyst in a single vat to break down the materials from polymers, which are large structures of repeating molecules bonded together, into individual molecules called monomers, which the microbes then ferment into a new type of biodegradable polymer that can be made into fresh commodity products. A One Earth paper describes the process.
“It’s sort of ironic because the purpose of using bio-based plastics is to be more sustainable, but it’s causing problems,” said first author Chang Dou, a senior scientific engineering associate at the Advanced Biofuels and Bioproducts Process Development Unit (ABPDU) at Berkeley Lab. Dou was recently named as one of the American Institute of Chemical Engineer’s 35 Under 35. “Our project is trying to get around the separation issue and make it so you don’t have to worry about whether you mix your recycling bin. You can put all the plastic in one bucket.”
In addition to streamlining recycling, the team’s approach could enable bio-based manufacturing of other valuable products using the same bacteria that are happily munching on plastic monomers. Imagine a world where biofuels or even medicines could be made from plastic waste — of which there is about 8.3 billion tons sitting around in landfills.
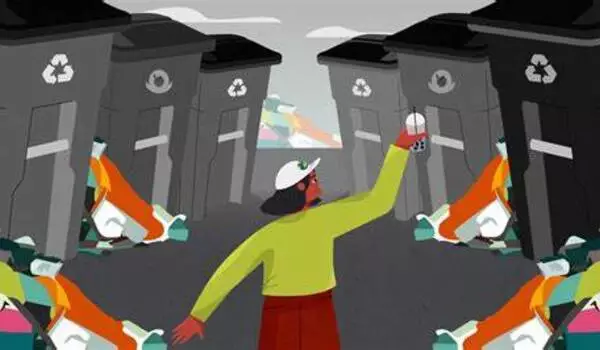
“There is an open discussion on whether we can use waste plastics as a carbon source for biomanufacturing. It is a very advanced idea. But we proved that using waste plastics, we can feed microbes. With more genetic engineering tools, microbes might be able to grow on multiple types of plastics at the same time. We foresee the potential to continue this study where we can replace the sugars, traditional carbon sources for microbes, with the processed hard-to-recycle mixed plastics that can be converted to valuable products through fermentation,” said Zilong Wang, a UC Berkeley postdoctoral researcher working at JBEI.
The next step for the Berkeley Lab scientists will be to experiment with other organic salt catalysts in order to find one that is both highly effective at breaking down polymers and can be reused in multiple batches to reduce costs. They are also simulating how the process would work on the large scales of actual recycling facilities.
The scientists demonstrated the potential of their approach in laboratory bench-scale experiments with mixtures of polyethylene terephthalate (PET), the most common petroleum-based plastic, used in things like water bottles and spun into polyester fibers, and PLA, the most common bio-based plastic, in their recent paper.
They used an amino-acid-based salt catalyst previously developed by colleagues at JBEI and a strain of Pseudomonas putida engineered by scientists at Oak Ridge National Laboratory. This combination successfully broke down 95% of the PET/PLA mixture and converted the molecules into a type of polyhydroxyalkanoate (PHA) polymer. PHAs are a new class of biodegradable plastic substitutes designed to efficiently break down in a variety of natural environments, unlike petroleum-based plastics.
Although their chemical recycling process is currently only proven for PET plastics contaminated with biodegradable PLA, team member Hemant Choudhary believes it would be beneficial for the diverse plastic streams encountered in real recycling facilities. “It can be completely integrated with existing plastic sources,” Choudhary, a Sandia National Laboratories staff scientist at JBEI, said. He explained that most commercial products are made up of a variety of different types of plastic. A fleece jacket, for example, is made with PET-based polyesters as well as polyolefins or polyamides.
“We can throw it in our one-pot process and easily process the polyester component from that mixture and convert it into a bioplastic. These monomers are soluble in water, but the leftover parts, the polyolefins or polyamides, are not.” The leftovers can be easily removed by simple filtration and then sent off for a traditional mechanical recycling process where the material is shredded and melted, said Choudhary.
“Chemical recycling has been a hot topic, but it’s difficult to make it happen on a commercial scale because all the separation steps are so expensive,” said Ning Sun, an ABPDU staff scientist and the project’s lead author and principal investigator. “However, by using a biocompatible catalyst in water, microbes can directly convert the depolymerized plastics without the need for additional separation steps.” These findings are very exciting, but we recognize that a number of improvements are still required to realize the developed process’s economic viability.”