Electrochemical actuators are devices that use electrochemical processes to convert electrical energy into mechanical energy. They’re used in soft robotics, artificial muscles, micropumps, sensors, and a variety of other applications. The development of flexible and stable electrode materials continues to be a major challenge.
A newly developed electrochemical actuator based on specialized organic semiconductor nanotubes is expected to be a game-changer for future researchers in robotics, bioelectronics, and biomedicine.
The development of an electrochemical actuator that uses specialized organic semiconductor nanotubes by University of Houston researchers represents a breakthrough in the field of materials science and engineering (OSNTs). The actuator, which is still in its early stages of development, will become an important part of research that will contribute to the future of robotic, bioelectronic, and biomedical science.
“Electrochemical devices that convert electrical energy to mechanical energy have the potential to be used in a wide range of applications, from soft robotics and micropumps to autofocus microlenses and bioelectronics,” said Mohammad Reza Abidian, associate professor of biomedical engineering at the University of Hawaii Cullen College of Engineering. He is the corresponding author of the study, “Organic Semiconductor Nanotubes for Electrochemical Devices,” which was published in the journal Advanced Functional Materials.
A newly developed electrochemical actuator using specialized organic semiconductor nanotubes is likely to become a key factor for future researchers in the fields of robotics, bioelectronics, and biomedicine.
An actuator is a machine component that is in charge of moving and controlling a mechanism or system, such as opening a valve. In layman’s terms, it is a “mover.” An actuator requires a control signal as well as an energy source. The control signal has a low energy level and can be generated by electric voltage or current, pneumatic or hydraulic fluid pressure, or even human power. Its primary source of energy could be an electric current, hydraulic pressure, or pneumatic pressure. When an actuator receives a control signal, it responds by converting the energy from the source into mechanical motion. It is a type of automation or automatic control in the electric, hydraulic, and pneumatic senses.
Significant movement (which scientists refer to as actuation and measure as deformation strain) and fast response time have long been elusive goals, particularly for electrochemical actuator devices that operate in liquid. This is because the drag force of a liquid restricts the motion of an actuator and limits ion transport and accumulation in electrode materials and structures. Abidian and his team refined methods for working around those two stumbling blocks in Abidian’s lab.
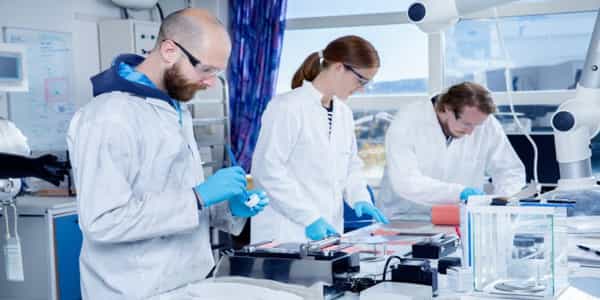
“Our organic semiconductor nanotube electrochemical device has a high actuation performance in liquid and gel-polymer electrolytes, with fast ion transport and accumulation and tunable dynamics. This device performs admirably, with low power consumption/strain, a large deformation, fast response, and excellent actuation stability “According to Abidian.
This exceptional performance, he explained, is due to the nanotubular structure’s massive effective surface area. The larger area allows for easier ion transport and accumulation, resulting in high electroactivity and durability.
“The low power consumption/strain values for this OSNT actuator, even when operating in a liquid electrolyte, represent a significant improvement over previously reported electrochemical actuators operating in liquid and air,” said Abidian. “We looked at long-term stability. When compared to previously reported conjugated polymer-based actuators operating in liquid electrolyte, this organic semiconductor nanotube actuator demonstrated superior long-term stability.”
Mohammad Javad Eslamian, Fereshtehsadat Mirab, Vijay Krishna Raghunathan, and Sheeran Majd from the UH Cullen College of Engineering collaborated with Abidian on the project. The organic semiconductors used were discovered in the 1970s by three scientists, Alan J. Heeger, Alan MacDiarmid, and Hideki Shirakawa, who was awarded the Nobel Prize in 2000 for their discovery and development of conjugated polymers.
For a new type of actuator to outshine the status quo, the end product must prove not only to be highly effective (in this case, in both liquid and gel polymer electrolytes), but also that it can last.
“We designed and built a micron-scale movable neural probe based on OSNT microactuators to demonstrate potential applications. This microprobe has the potential to be implanted in the brain, where neural signal recordings that are hampered by damaged tissue or neuron displacement can be improved by adjusting the position of the movable microcantilevers “Abidian stated.
The next step will be animal testing, which will begin shortly at Columbia University. Early results are expected by the end of 2021, followed by longer-term tests. “Given our achievements thus far, we anticipate that these new OSNT-based electrochemical devices will aid in the advancement of the next generation of soft robotics, artificial muscles, bioelectronics, and biomedical devices,” Abidian said.