As part of a bigger attempt to cut the cost of spaceflight, the United States military has granted contracts under a new initiative to address in-space manufacturing demands. Space manufacturing could enable humans to construct enormous structures more effectively, using resources delivered from Earth or gathered on other planets such as the moon or Mars. Such work could start on the moon in the near future, especially with the coming of private landing missions as part of NASA’s Commercial Lunar Payload Services program.
Manufacturing in space is still in its infancy, and the US military wants to help it along. DARPA officials claimed a few weeks ago that the Defense Advanced Research Projects Agency (DARPA) recently began work with eight teams to provide proofs of concept “to enable construction of future space structures on orbit without the volume limits imposed by launch.”
DARPA officials stated the NOM4D program, which stands for “Novel Orbital Moon Manufacturing, Materials, and Mass Efficient Design,” will test materials science, manufacturing, and design capabilities that could be deployed off Earth eventually. (However, the initial phases funded today will not be in space.)
While NOM4D does not immediately explore technology for use on or near the moon, DARPA officials noted that the Earth-orbiting structures that the program intends to enable and evaluate could someday allow the US military to monitor cislunar (Earth-moon) space. Given the rising commercial and government activity in this zone, the United States military considers cislunar space to be a priority.
Currently, all space systems are developed, produced, and tested on Earth before being launched into a stable orbit and deployed to their final operational configuration. These limits are especially severe for large structures like solar arrays, antennas, and optical systems, where size is important to performance.
Bill Carter
As DARPA pointed out, the problem with launching things into space is that such objects are confined by the dimensions and lift capability of the rocket, not to mention the vibrations. This is why antennas, for example, are frequently unfolded in orbit; they are too large to launch otherwise.
“Currently, all space systems are developed, produced, and tested on Earth before being launched into a stable orbit and deployed to their final operational configuration,” said Bill Carter, NOM4D program manager at DARPA’s defense sciences office, in the same statement. “These limits are especially severe for large structures like solar arrays, antennas, and optical systems, where size is important to performance.”
More complicated constructions in orbit will almost certainly have to be built in place, similar to how the International Space Station was assembled piece by piece. However, unlike the ISS, which required people to do dozens of spacewalks with the help of the Canadarm2 robotic arm, future in-space industrial facilities will almost certainly rely nearly entirely on robotic technologies. Furthermore, future facilities will be required to use raw materials rather than preassembled components like those found on the ISS.
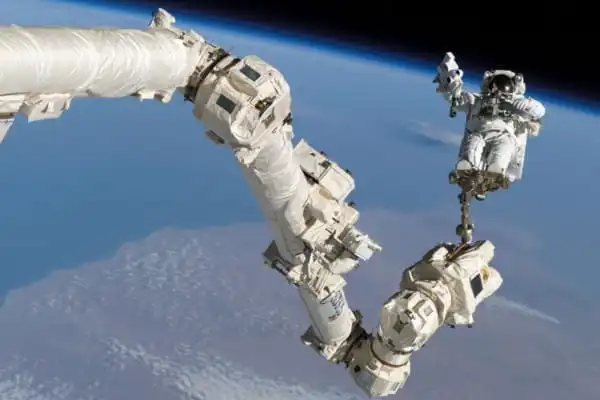
DARPA stressed that the NOM4D program does not seek to launch raw materials into orbit, collect lunar samples, or construct any buildings at this time. The program will allow for potential “orbital experimentation” in “potential follow-on efforts” in the next 10 to 20 years, the agency stated. For now, however, there are three initial phases planned.
“During Phase 1, program participants are charged with meeting strict structural efficiency requirements supporting a megawatt-class solar array,” according to DARPA. “Teams are tasked with increasing mass efficiency and demonstrating precision production for radio frequency reflectors in Phase 2. The final phase requires performers to demonstrate precision for infrared reflectors.”
According to DARPA, the full list of in-space materials and manufacturing receivers and their missions is as follows:
- HRL Laboratories, LLC, Malibu, California, is working on innovative die-less fabrication procedures for orbital mechanical elements and bonded structures.
- Gainesville, Florida-based University of Florida is creating predictive material and correlative process models to enable on-orbit laser shaping.
- The University of Illinois Urbana-Champaign in Champaign, Illinois, is working on a high precision in-space composite forming technique based on self-energized frontal polymerization.
- Physical Sciences, Inc., Andover, Massachusetts, is working on the continuous manufacture of regolith-derived glass-ceramic mechanical structures for large-scale orbital applications.
- Teledyne Scientific Company, LLC, Thousand Oaks, California, is developing a comprehensive materials characteristics database of additive-modified regolith for use in precision orbital structures with controlled thermal expansion.
The list of mass-efficient designs for in-space manufacturing recipients and their tasks, in DARPA’s words, is:
- The University of Michigan, Ann Arbor, Michigan, is investigating new design techniques based on metamaterial and metadamping principles for mass-efficient, high-precision, stable, and durable space structures.
- Opterus Research and Development, Inc., Loveland, Colorado, is designing extreme mass efficient large-scale structures that are designed for robustness and mobility.
- The California Institute of Technology in Pasadena, California, is developing novel tension and bending hybrid topologies and structural components with highly anisotropic mechanical response.