Carbon capture is critical for reducing the impact of human CO2 emissions on our climate. Researchers at Japan’s University of Tokyo and Nagoya University have developed a method to determine whether the carbon in concrete comes from raw materials or from carbon in the air that is trapped when it reacts with the concrete to form the mineral calcium carbonate.
The team was able to successfully verify direct air carbon capture by measuring the ratio of certain carbon isotopes in concrete that had been exposed to air and concrete that had not. This method could be beneficial to the industrial sector and countries looking to reduce their carbon footprint.
2023 is on track to be the hottest year on record. Rice crops in Japan wilted, and roads in the United States melted. Despite international agreements and calls to action, emissions of greenhouse gases from fossil fuels have continued to rise. We must do more to keep the planet from exceeding the critical 2-degree Celsius temperature rise threshold by 2100 (compared to preindustrial levels). According to the Intergovernmental Panel on Climate Change, reducing and preventing future emissions is insufficient. If we are to meet our goal, we must also remove carbon dioxide from the atmosphere.
Concrete has long been known to react with CO2 in the air to form calcium carbonate, an undesirable phenomenon because it induces corrosion of the steel bars inside concrete structures. However, the concrete industry is now considering ways to make effective use of this reaction.
Professor Ippei Maruyama
Direct air capture (DAC) uses chemicals or physical processes to remove carbon dioxide from the atmosphere. Increasing the use of DAC technologies is part of the International Energy Agency’s (IEA) net-zero emissions scenario, which proposes a set of methods to allow the global energy sector to remove as much CO2 (CO2) as it emits by 2050. According to the International Energy Agency, industry will be responsible for one-quarter of global energy system CO2 emissions in 2022. Cement is the second most common industrial product (after water), and it has a high environmental impact.
“As much as 800 kilograms of CO2 is emitted per ton of cement during its production, so reducing emissions has become a significant issue in the concrete industry,” explained Professor Ippei Maruyama from the Department of Architecture at the University of Tokyo Graduate School of Engineering. “Concrete has long been known to react with CO2 in the air to form calcium carbonate, an undesirable phenomenon because it induces corrosion of the steel bars inside concrete structures. However, the concrete industry is now considering ways to make effective use of this reaction.”
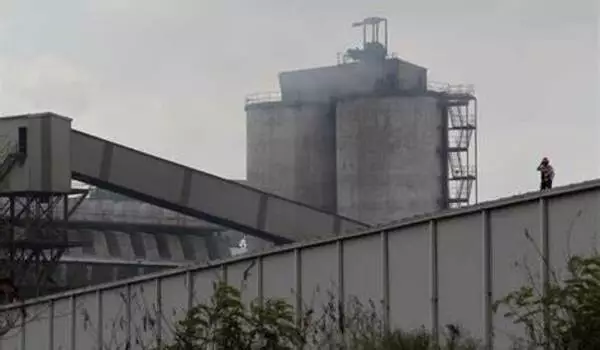
Although problematic for construction, the reaction that causes calcium carbonate to form fixes or traps CO2, removing the gas from the atmosphere. Calcium carbonate is also found naturally in rocks, such as limestone, which are used in concrete manufacturing. “This makes it difficult to distinguish whether or not CO2 identified in concrete has been freshly extracted from the air or comes from rocks,” said Maruyama. “So we developed a method to verify this, which could be used to determine whether the concrete produced can be certified as offsetting CO2 emissions.”
The study was carried out by creating hydrated cement paste samples as a concrete replica. They ground the paste sample into powder after it had been sufficiently hydrated, keeping the nonexposed powder contained and the exposed powder exposed to the air. After seven and 28 days, they dissolved the powder in acid to collect the gas and analyzed the ratio of several carbon isotopes (atoms with the same chemical properties but different physical properties), namely carbon-12, carbon-13, and carbon-14, using a technique known as accelerator mass spectrometry.
This enabled the team to evaluate where the carbon came from, and whether it was already present in the raw materials, as the carbon ratios reflected the known proportion of carbon isotopes in the air at the time the gas was sealed.
The researchers plan to apply this lab-based method to real-world locations to see how different amounts of raw materials used in local concrete production affect the results. “Because removing carbon dioxide from the atmosphere is certified as an act of CO2 offset, it is economically valuable in terms of emissions trading.” Digging up calcium carbonate for use in concrete is not, so the distinction is critical, and this research can help to support a healthy market,” Maruyama explained. “We believe that the carbon neutrality and a circular economy in the construction industry are essential to our future, particularly in Japan where this industry has a role in supporting business continuity and recovery from natural disasters.”