Capacity requirements planning (CRP) is a strategy or application used mostly by manufacturing organizations to determine their capacity to meet their production targets. The CRP approach evaluates a company’s anticipated manufacturing schedule first. The company’s real production capabilities are then weighed against this timetable to assess if the current capacity can successfully match the existing production schedule.
CRP shows businesses how many goods they can produce per hour, per day, and per month based on the number of employees, workstations, and other factors. The maximum amount of work that an organization is capable of doing in a particular period is referred to as design capacity in the context of capacity planning. Due to constraints such as quality issues, delays, and material handling, an organization’s effective capacity is the maximum quantity of work it can complete in a given period.
Capacity requirements planning is the process by which a manufacturing business determines how much product it needs to manufacture and whether it will be able to reach its production targets. It’s a technique for determining the “ability of present resource levels to meet current orders and projected demand” in the short term.
CRP also aids in identifying where and when utilization issues may arise, allowing for the implementation of preventative/alternative interventions. Certain pieces of information are required to conduct a CRP. To figure out how many available work hours you have, you’ll need to know how many people you have, how many hours each employee can work, how many machines you have, and how efficient they are, among other things.
CRP can also be thought of as a management technique that focuses on maximizing a company’s resources by accurately estimating output goals. CRP also refers to detailing the estimation for each process based on the order manufacturing, making modifications, and then planning the work of each process so that the firm may reach its target without exerting additional effort.
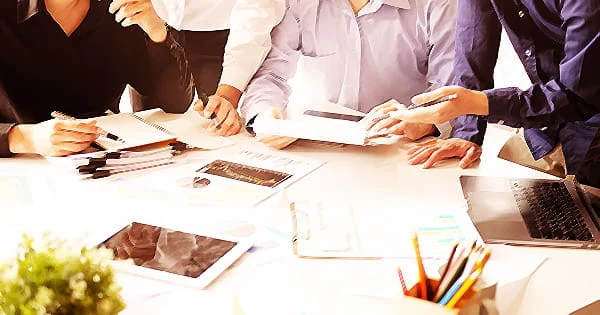
Inefficiency is caused by a mismatch between an organization’s capacity and its customer’s demands, which results in underutilized resources or unmet customer demand. The purpose of capacity planning is to reduce this disparity as much as possible. If a company’s production capacity is insufficient, it may change its production goals or take other efforts to align expectations with capacity, such as contracting with another company with excess capacity to handle its output.
Materials, machine production time, machine changeover time and tooling, maintenance and downtime, as well as human availability and skill, may be considered by the operations manager in order for shift work to be assigned and resources to be used efficiently. Changes in production output, such as increasing or lowering the production amount of an existing product or producing new items, affect demand for an organization’s capacity.
The ability to plan for the future is critical to a company’s success. Without a good plan in place, a business owner risks running into unanticipated problems, some of which might have a negative impact on the company’s bottom line. The operational team will inform the planning team of their capacity to achieve the planning requirements, and the planning team will then work with the procurement team to ensure that materials or components required for the production process are made available on schedule and in full.
After that, the planning team will confirm the capacity and material requirements plans and issue a work order, which will be forwarded on to the production team. However, sectors with significant seasonal sales, such as retail stores (selling raincoats and sweaters) or agricultural products companies, may need to re-evaluate their capacity requirements more frequently than enterprises with consistent revenue.
When you can’t match client demand, you risk losing customers to the competitors. CRP can assist a company decide how much to invest in its personnel, materials, and equipment in the long run. If a capacity requirement plan is not followed in a manufacturing process, a company may commit to making goods for which it lacks the resources to produce the finished product to the needed specifications, on time and in full.
Discrepancies between capacity estimations and actual manufacturing output can lead to a scarcity of items or workers, causing extensive delivery delays or even leaving some customers’ orders unmet entirely. The capacity plan is an important part of the planning process since it determines how the product will be routed through the plant to its finished state, as well as the financial ramifications of doing so.
Types of Capacity Requirements Planning (CRP) –
- Lead Strategy: The corporation expands its basic capacity in anticipation of increased demand for its products and services under this strategy. The lead approach is typically used to woo clients from your competitors to you by shortening your lead time. The benefit of a lead strategy is that even during peak sales periods, the company will have enough product/service capacity to meet all demand.
- Lag Strategy: This method is employed when a company’s capacity has been reached or exceeded owing to increased demand. This method reduces the likelihood of a product or service going to waste. Although there is a strong possibility that it may result in the loss of potential clients due to stock-outs or poor service standards (you may not be able to fulfill the sudden rise in demand hence losing your customers to competitors).
- Match Strategy: The most ingenious capacity planning approach, but also the most challenging to implement. Rather of significantly increasing capacity in response to anticipated or actual increases in demand, the company’s capacity is just tweaked or enhanced in response to changing market conditions.
Some businesses, on the other hand, may opt to use off-the-shelf software to aid with the implementation of their CRP. Increase capacity through introducing new processes, equipment, and materials, increasing the number of people or machines, increasing the number of shifts, or acquiring additional manufacturing facilities. CRP software can develop a personalized production plan that includes personnel, materials, systems, and other resources based on data supplied by management.