Bio-based thermoplastics can be recycled after use and are made from organic, renewable resources. Blending bio-based thermoplastics with other thermoplastics can increase their durability. To obtain the best qualities, the material-to-material contact in these mixes occasionally needs to be improved.
At BESSY II, a group from the Netherlands’ Eindhoven University of Technology has now examined how a novel method makes it possible to create thermoplastic blends with a high interfacial strength from two base materials: The formation of nanocrystalline layers throughout the procedure improves material performance, according to images captured at the IRIS beamline’s new nano station.
Since bio-based thermoplastics are made from non-petroleum raw sources and are recyclable like regular thermoplastics, they are regarded as ecologically benign. Polylactic acid (PLA), a thermoplastic base material, can be made from corn or sugar cane. The qualities of PLA-based polymers are being optimized by researchers worldwide, for instance, by combining them with other thermoplastic base materials. This is a true struggle, though.
By elucidating the location and distribution of the crystalline layer in our samples, we could understand the procedure of mixing much better. By developing a new strategy we have cleared a path for the development of high-performance polymer blends.
Hamid Ahmadi
A new process for better blends
A group from TU Eindhoven, under the direction of Professor Ruth Cardinaels, is now demonstrating how PLA may be effectively combined with another thermoplastic. They created a method wherein certain PLA-based copolymers, like SAD, are created during manufacture. This allows the two raw materials to be mixed more easily because it creates extremely stable (stereo)-crystalline layers at the interfaces between the various polymer phases (ICIC approach).
Insights at the IRIS-Beamline
At BESSY II, they have now discovered which processes ensure that the mechanical properties of the mixed thermoplastic are significantly better. To do so, they examined pure 50% blends of the thermoplastics PLA and polyvinylidene fluoride (PVDF) as well as samples with the PLA-based copolymers at the IRIS beamline of BESSY II.
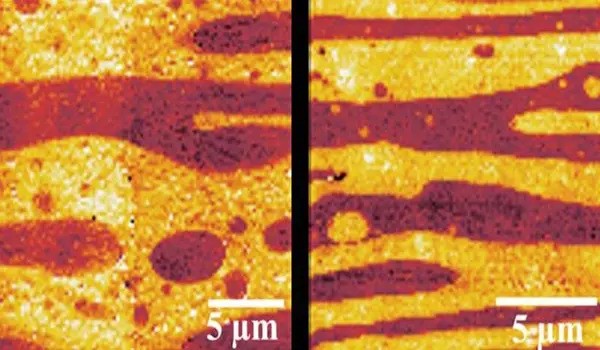
Stereocomplex crystals at the interfaces
Hamid Ahmadi, a PhD student, was able to show how the PLA-based copolymer SAD forms using infrared spectroscopy on the IRIS beamline. Additional X-ray observations demonstrated the impact of SAD formation on the crystallization behavior. Advanced chemical visualization and identification from sample areas as tiny as 30 nm is made possible by the new nano imaging and spectroscopy capabilities at the IRIS beamline. Determining that the stereocomplex crystals are only found at the interface required this level of accuracy. Images from infrared nanoscopy revealed a layer of stereocomplex crystals at the interfaces that was 200–300 nm thick.
Reason for more stability
The stability and crystallization temperature are raised by the stereocomplex crystals that form at the interfaces. The PLLA/PVDF blend’s overall crystallization process is accelerated by nucleation at the interface. Furthermore, the interfacial crystalline layer enhances the tensile characteristics by improving the transmission of mechanical stresses between the phases; the elongation at break even can rise by as much as 250%.
“By elucidating the location and distribution of the crystalline layer in our samples, we could understand the procedure of mixing much better,” Hamid Ahmadi states. “By developing a new strategy we have cleared a path for the development of high-performance polymer blends,” says Ruth Cardinaels.