Barrel plating is a form of electroplating used for plating a high volume of smaller metal objects in one sitting. It is normally used for plating smaller parts and entails placing the objects in a specially constructed vessel, commonly referred to as a barrel. It consists of a non-conductive barrel-shaped cage in which the objects are placed before being subjected to the chemical bath in which they become plated. It is an efficient way of plating due to its low cost and the fact that it is ideal for large runs of parts that are small and durable.
Barrel plating is an electroplating process by which articles are brought into contact with an electrolyte while rotating in a perforated hardwood barrel.
An important aspect of the barrel plating process is that the individual pieces establish a bipolar contact with one another— this results in high plating efficiency. The barrel contains center bars that conduct the electrical current. However, because of the large amount of surface contact that the pieces have with each other, barrel plating is generally not recommended when precisely engineered or ornamental finishes are required.
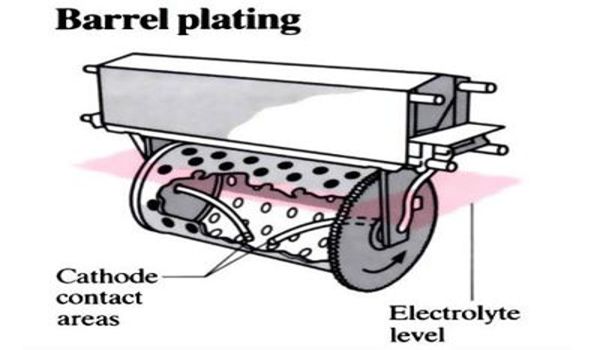
The barrel slowly rotates while immersed in the electrolytic plating solution. This causes the parts to tumble or “cascade,” which provides an even, uniform coating application. Barrel plating of tin is extremely cost-effective, although it takes a relatively long time to complete the plating process. Typical barrel plating applications include enhancing corrosion protection, increasing aesthetic appeal, and producing and engineering finish that protects the parts against wear and tear.
Barrel plating began as a practice in the United States during the US Civil War. Until the 1940s, there were no significant improvements in barrel plating; however, after WWII, chemically resistant plastics were available for manufacturing the barrel plating systems. The harsh chemicals required, however, meant that it had to await the development of non-conductive and chemically resistant plastics— primarily perspex and polypropylene— before it could receive widespread use. It a process in which components are placed in an electrolyte solution in a barrel then rotated or tumbled to provide an even coat–was discarded because of the fragility of the components. By 2004, however, barrel plating had become widespread: it was estimated that as much as 70% of modern electroplating facilities used barrel plating techniques at that time.
Barrel plating offers a cost-effective means of plating a high volume of small, durable parts such as stampings and fasteners. It also works well for plating parts of various shapes and sizes. High, medium, and low-efficiency barrels for plating are available, resulting in improved deposit distribution that is used to apply corrosion resistance and high-tech conductive and solderable/bondable functionality.
Information Source: