Jonathan Tan and Roger Basu were looking for an area where they could apply their thin-film technology knowledge and make the greatest and fastest impact feasible five years ago. They went with batteries, namely battery degeneration, and longevity. It wasn’t — and still isn’t — a sector devoid of investment, research, or firms claiming to have discovered the next big thing in batteries. However, the duo claims to have zigzagged where everyone else has zagged.
Tan and Basu, who co-founded the California-based business Core-shell in 2017, said they avoided trying to design a new battery from the ground up, which would have been a costly and time-consuming endeavor that many companies were already working on. Instead, they concentrated their efforts on nanolayer coating technology, which can be integrated into an existing battery cell manufacturing system. According to the Core-shell creators, this covering boosts useable battery capacity by 30% or more and enhances heat tolerance by 200 percent, all while cutting costs and enhancing safety. It may also be used with a variety of chemistries and applications, including consumer electronics and electric cars.
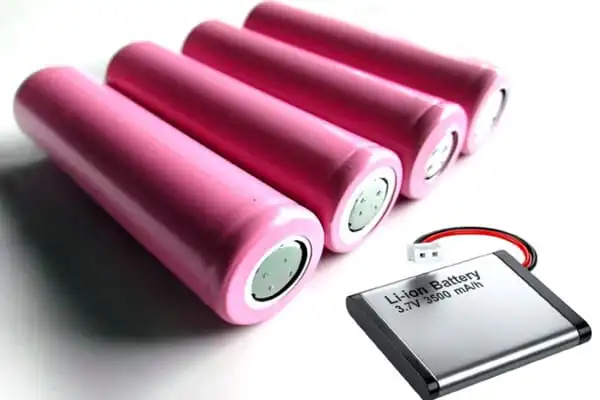
Core-shell CEO Tan told TechCrunch, “We aim to be the ‘Intel Inside’ of batteries.” “We intend to use this coating technique directly on the most problematic parts inside the battery, such as the anode’s surface and the cathode’s surface where it meets the electrolyte,” says the researcher. Several investors, battery makers, and even the legendary dune buggy brand Meyers Manx have backed Coreshell’s revolutionary concept. Tesla co-founder Marc Tarpenning, Chunmei Ban, a professor at the University of Colorado renowned for her work at the National Renewable Energy Laboratory, and Judith O’Brien, who has built a career out of assisting firms with their initial public offerings, are among its advisers.
The two bootstrapped the firm at first, then went through the Alchemist Accelerator in 2020 to seek startup capital. Since then, Coreshell has begun working with BASF on a variety of coatings for improved cathode materials, as well as demonstrations with other battery cell manufacturers that Tan declined to identify. Trousdale Ventures, Industry Ventures, and Helios Capital Ventures recently led a $12 million Series financing for the startup. The round included existing investors Entrada Ventures, Foothill Ventures, and Asymmetry Ventures. To date, Coreshell has raised $19 million.
Meyers Manx was formed as a result of Coreshell’s association with Trousdale Ventures and, more notably, managing partner Phillip Sarofim. The Coreshell technology will be installed “within” a prototype Meyers Manx electric beach buggy. The relationship fits into Meyers Manx’s objective to “continue offering adventure and enjoyment to the globe, but with even greater performance capabilities to satisfy the demands of modern-day customers,” according to Sarofim, who is also chairman of Meyers Manx.
Coreshell can demonstrate its full capabilities both at the cell and device level, as well as the speed with which it can be applied to vehicles, thanks to the Meyers Manx demonstration and collaborations with other battery cell manufacturers and automakers, according to Tan, a chemical engineer, turned technical business development executive. New Era Converting Machinery is also helping the firm show how its thin-film coating technology may be employed in roll-to-roll production. Coreshell may be able to persuade automakers and cell manufacturers to use their technology if it is successful.
Roll to roll is a continuous process used by battery manufacturers. Tan said that when you cut apart a cylindrical cell, you’ll see a jelly roll of electrodes. These are simply big rolls of electrodes on foil before they’re inserted into the battery casing. “Obviously, it’s much smaller, to begin with,” Tan explained, “but even demonstrating that capability is a key step toward being able to show that, ‘Hey, you can slot us right in and get the performance enhancements of solving battery degradation and having increased capacity while lowering manufacturing costs.”