Heat exchangers are used in both cooling and heating processes to transfer thermal energy from one medium to another. As a result, they are used in numerous applications and industries, including energy, water, manufacturing, transportation, construction, electronic, chemical, petrochemical, agriculture, and aerospace. Heat exchanger designs have remained largely unchanged for decades. According to the researchers, recent advances in 3D printing enable the production of previously thought-impossible three-dimensional exchanger designs.
Researchers at the University of Illinois Urbana-Champaign are demonstrating next-generation energy technology by designing ultra-compact, high-power heat exchangers using topology optimization and metal 3D printing. Heat exchangers are used in almost every major industry, including energy, water, manufacturing, transportation, construction, electronic, chemical, petrochemical, agriculture, and aerospace.
Heat exchanger designs have remained largely unchanged for decades. Recent advances in 3D printing enable the production of previously thought-impossible three-dimensional exchanger designs. These new and innovative designs are significantly more effective and efficient, but they necessitate the use of specific software tools and design methods in order to manufacture high-performance devices.
Demonstrating next-generation energy technology, researchers are using topology optimization and metal 3D printing to design ultra-compact, high-power heat exchangers.
Metal 3D Printing is a laser-based technology that uses metal powders. A high-powered laser, similar to Laser Sintering, selectively binds together particles on the powder bed while the machine distributes even layers of metallic powder. It is currently used in industry to manufacture tool components and finished parts in industries such as aerospace and automotive. 3D printing can be used to create aircraft components or rocket motors, saving weight and money.
Recognizing the need to develop new, high-performance heat exchangers, Grainger College of Engineering researchers have created software tools that allow for new 3D heat exchanger designs. These new and innovative designs are significantly more effective and efficient, but they necessitate the use of specific software tools and design methods in order to manufacture high-performance devices.
“We created shape optimization software to design a high-performance heat exchanger,” said William King, co-study leader, and professor of Mechanical Science and Engineering at The Grainger College of Engineering. “We can use the software to identify 3D designs that are significantly different and better than conventional designs.”
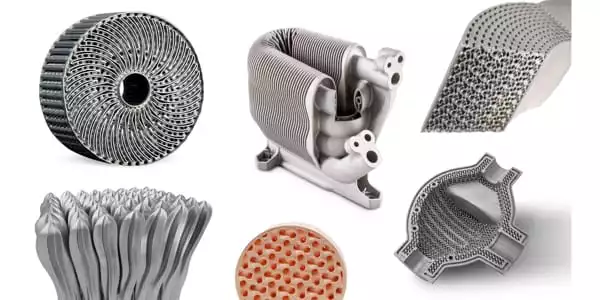
The researchers began by investigating a type of exchanger known as a tube-in-tube heat exchanger, in which one tube is nested inside another. Tube-in-tube heat exchangers are widely used in water treatment and building energy systems. The researchers designed internal fins (only possible with metal 3D printing) using a combination of shape optimization software and additive manufacturing.
The researchers began by looking into a tube-in-tube heat exchanger, which consists of one tube nestled inside another. Tube-in-tube heat exchangers are widely used in drinking water and building energy systems. The researchers used a combination of shape optimization tools and AM to create fins (which are only possible with metal 3D printing) inside the tubes. According to the researchers, they designed, built, and tested an optimized tube-in-tube heat exchanger. Their optimized heat exchanger has a volumetric power density that is roughly 20 times that of a current state-of-the-art commercial tube-in-tube device.
“We designed, fabricated, and tested an optimized tube-in-tube heat exchanger,” said Nenad Miljkovic, co-study leader and associate professor of Mechanical Science and Engineering. “Our optimized heat exchanger has a volumetric power density that is approximately 20 times greater than a current state-of-the-art commercial tube-in-tube device.”
Heat transfer is a pervasive problem that is central to the First Law of Thermodynamics. Simply put, a heat exchanger is a device that efficiently transfers heat between two (or more) fluids, typically a liquid-liquid, liquid-gas, gas-gas, or multiple fluids. They can be found in products such as air conditioners and automobile engines.
With billions of heat exchangers in use worldwide today and increased emphasis on the need to reduce our reliance on fossil fuels, compact and efficient heat exchangers are in high demand, particularly in industries where heat exchanger size and mass have a significant impact on performance, range, and costs.