Electroplating is a process in which an electric current is used to deposit metal onto a workpiece. Mechanical plating, also known as peen plating, mechanical deposition, or impact plating, is a plating process that imparts the coating by cold welding fine metal particles to a workpiece. In the process, the workpiece to be plated is the cathode of the circuit and the metal to be plated on the workpiece is the cathode.
Mechanical plating refers to an industrial process that involves the application of a coating to a substrate material by cold welding small metal particles to it.
Mechanical galvanization is an intriguing application technique and has been a commercially accepted process within the North American and European finishing industries for almost half a century. It is the same process but applies to coatings that are thicker than 0.001 in (0.025 mm). It is commonly used to overcome hydrogen embrittlement problems. During its history, it has also been referred to as peen plating, impact plating, and mechanical galvanizing. Commonly plated workpieces include nails, screws, nuts, washers, stampings, springs, clips, and sintered iron components. These products are supplied to diverse markets such as the automotive, aerospace, and construction industries.
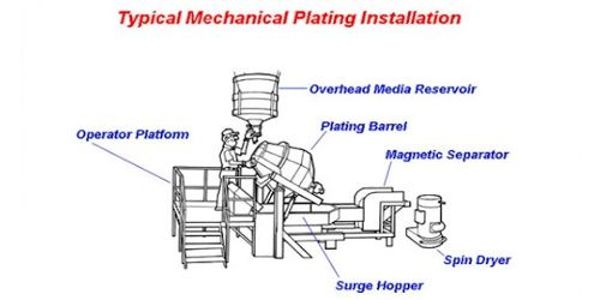
Mechanical plating is an alternative coating system for the impact deposition of zinc and other ductile metals. The process involves tumbling the workpieces with a mixture of water, metal powder, media, and additives. The mechanical plating technique is essentially a batch process for the bulk coating of small parts such as fasteners, washers, springs and spring clips, steel stampings, and nails. Common coating materials are zinc, cadmium, tin, copper, and aluminum.
Invented by the Tainton Company in the 1950s, it was further developed by the 3M company.
Process
The process begins with descaling and removing soil from the workpiece. This technology is an effective means of applying one metal over another as a coated deposit without using an electrical current. This can be done in the tumbler or in a separate cleaning system. After cleaning, the parts are prepared by combining them with water, medium, and a surface conditioner. The surface conditioner lightly coats the workpiece in copper, while the medium removes any residual mill scale or oxides. It is used to apply a number of metallic deposits such as zinc, cadmium, copper, tin, aluminum, and other mixed alloys onto a wide range of substrates.
Finally, accelerators, promoters, and metal powder are added to the mix. The accelerators and promoters provide the proper chemical environment for the plating to occur, such as the maintenance of a pH level of 1 to 2 to prevent oxidation and promote adhesion. The medium that is already in the mixture cold welds the metal powder to the workpiece through impacts that are induced by the tumbling action of the tumbler.
At this point the surface finish is typically matte to a semi-bright finish, however, the finish can be improved with a water polish. The time required for the above process is approximately 50 minutes. Mechanical deposits can be characterized to some extent by their relative thickness. Standard plating builds are typically 8-12 microns, which compete against coatings applied by electrodeposition.
This process works better if the workpieces’ surface finish is slightly rough. It is a form of metal galvanization used to prevent corrosion and hydrogen embrittlement.
Information Source: