It is very expensive to fire bricks and make mortar and cement, but organic chemists at Flinders University are developing more sustainable alternatives, focusing on building materials made from waste products.
In another step toward the circular economy, Flinders Chalker Lab researchers used low-cost feedstocks to create lightweight but durable polymer building blocks that can be bonded together using an adhesive-free chemical reaction. Their most recent study investigated the strength of these materials and how they can be reinforced in construction.
Matthew Flinders Professor of Chemistry, Justin Chalker, says the need to develop sustainable building materials is increasingly important, with cement, iron, and steel production accounting for more than 15% of global CO2 emissions each year.
“We tested a new type of brick made from waste cooking oil mixed with sulfur and dicyclopentadiene in this study (DCPD). Sulfur and DCPD are both byproducts of the petroleum refining process. When a trace amount of amine catalyst is applied to the bricks, they bond together without the use of mortar. All of the raw materials are abundant and can be classified as industrial waste. This study is part of a larger effort to create a more sustainable built environment” Professor Chalker, project leader, says.
We tested a new type of brick made from waste cooking oil mixed with sulfur and dicyclopentadiene in this study (DCPD). Sulfur and DCPD are both byproducts of the petroleum refining process. When a trace amount of amine catalyst is applied to the bricks, they bond together without the use of mortar.
Professor Chalker
For further development, the Chalker Lab’s new polymer research team at Flinders University’s College of Science and Engineering is collaborating with Clean Earth Technologies. Scaling up and potential commercialization
Clay is one of the most common natural mineral materials on the planet. Clay must have certain properties and characteristics in order to be used in brick manufacturing. Such clays must be plastic, allowing them to be shaped or molded when mixed with water; and they must have sufficient wet and air-dried strength to hold their shape after forming. Furthermore, when heated to the proper temperatures, the clay particles must fuse together.
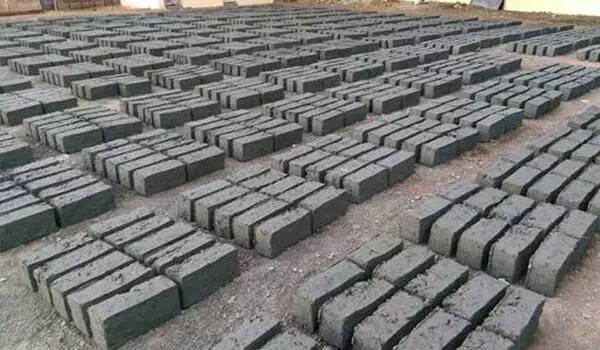
A brick, one of society’s building blocks, made from our waste. Nzambi Matee of Nairobi, Kenya is the inventor of the plastic brick, which almost sounds too good to be true. Contrary to popular belief, plastic bricks are twice as strong as concrete, and their performance is optimized. The bricks are made of sand and plastics. Sand and plastic are mixed at extremely high temperatures before being compressed into bricks.
The fundamentals of brick production have remained constant over time. However, technological advancements have made modern brick plants significantly more efficient and have improved overall product quality. A more complete knowledge of raw materials and their properties, better control of firing, improved kiln designs, and more advanced mechanization have all contributed to advancing the brick industry.
The latest study, published as a cover feature in a special issue on Sustainability in the journal Macromolecular Chemistry and Physics, expanded the research to test the new bricks’ mechanical properties and look at ways to reinforce them in construction, including with carbon fibre fillers.
According to Dr. Maximilian Mann, a Chalker Lab research associate, in addition to repurposing waste materials into value-added construction materials, the polymer bricks’ sulfur-sulfur bond allows them to be bound together without mortar, unlike traditional building methods.
“The bonding in this novel catalytic process is very strong,” Dr. Mann says, “producing a sustainable construction material with its own mortar that will potentially streamline construction.” According to the study’s first author, Paris Pauling, the study is an excellent example of new scientific developments in sustainable materials science.