Engineers are working on a novel way to enhance soft plastic recycling by constructing a smart robot that can recognize, sort, and separate various forms of recyclable garbage. Industries that employ recycled trash as feedstock for production have waste contamination standards, thus garbage must be separated. Plastics cannot be combined with paper, metal, or glass if they require plastics for their production processes. If a substance is polluted, it cannot be utilized and must be disposed of in a landfill.
Despite recent improvements in plastic recycling, waste is becoming a bigger problem. Soft plastics such as cling wrap and plastic bags are a major source of pollution, with 94 percent of them ending up in landfills in 2016-17. Soft plastics are difficult to recycle because they tangle readily in trash sorting gear, causing mechanical failure and contamination of other recyclable materials like paper.
Due to this issue, existing recycling systems rely on hand sorting of soft plastics, which is a time-consuming and dangerous operation. Soft plastic is difficult to recycle since it is difficult to differentiate from paper. Soft plastics can also become stuck in machinery and produce blockages when being processed. Soft polymers can become entangled in machinery, causing malfunctions and industrial downtime.
As a result, only a tiny fraction of soft plastics, around 6%, gets processed, and existing technology solutions are insufficient. Researchers from the University of Sydney’s Centre for Internet of Things (IoT) and Telecommunications are developing a unique method to increase soft plastic recycling by creating a smart, automated robotic system that uses robotics and AI to sort recyclable waste as part of a federal government Cooperative Research Centre Project grant.
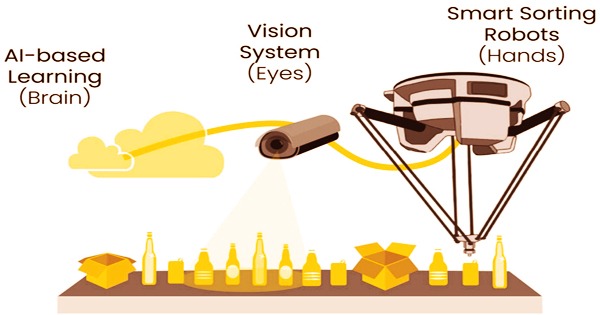
From the School of Electrical and Information Engineering, Professor Branka Vucetic, Professor Yonghui Li, Associate Professor Wanli Ouyang, Dr. Wanchun Liu, and Senior Technical Officer Dawei Tan are part of the team.
“The recycling robotic automation system will use artificial intelligence and computer vision to learn how to identify different forms of recycling waste, effectively learning how to ‘see’ and ‘sort’ waste, to create separate waste streams and maintain soft plastics’ purity so they can be recycled,” said IoT expert, Professor Branka Vucetic.
“Soft plastics are a major contributor to landfills and have long been a problem for the circular economy and waste management sectors due to a lack of a suitable and safe sorting process. Using the latest IoT techniques, we have created a custom robot to solve this issue,” said Professor Yonghui Li.
Not only is the system we built based on robotics, but it is also the world’s first IoT system. It’s worth noting that the majority of existing soft plastic recycling options rely on human sorting. The team was motivated to create a procedure that resembled that of a person. As a result, they created an IoT system that operated similarly to a person. They have 3D cameras that act as human eyes, communication networks that act as human nerves, artificial intelligence (AI) that acts as the human brain, and a robot arm that acts as the human arm.
“Between 2018 and 2019, Australia generated 2.5 million tons of plastic waste, which included soft plastics: Only 9 percent was sent to recycling while 84 percent went to landfill. We aim to drastically switch those percentages by developing a solution that allows for most soft plastic waste being recycled,” said Dr. Wanchun Liu.
To create the system, the researchers are collaborating with trash management firms IQRenew and CurbCycle, as well as technology developers Licella, Mike Ritchie and Associates, and Resource Recovery Design. The technology sees using 3D cameras that are coupled with computer vision and artificial intelligence. It’s a self-learning process, so once they’ve seen enough photos, they’ll be able to figure out what they need to know. Machine learning is used to assist this system.
AI is also used to train the robot to pick up things accurately, at the right angles and at the right place; the speed must be coordinated with the conveyor belt’s movement. “Not only does our project divert household soft plastics from going to landfill; by creating a solution for the collection and sorting of waste with our industry and research partners, we’re also creating a sustainable supply chain that takes rubbish from households to end markets,” said Associate Professor Wanli Ouyang.
“The robot will identify ‘CurbyTagged’ bags and differentiate sources of plastic, separating soft plastics from the fully co-mingled recyclables,” he said.
This method is used in conjunction with household collecting. The procedure is set up to be a collaborative effort between local governments and waste recovery facilities. Councils will give special bags to residents, who will then collect soft plastics and place them in these bags. These bags will be collected from recycling bins and delivered to MRFs alongside other mixed trash. The soft plastics will be separated from other trash and utilized for a variety of purposes, including advanced recycling into oils and other valuable chemicals utilizing Licella Holdings’ patented Catalytic Hydrothermal Reactor technology (Cat-HTR).
Professor Thomas Maschmeyer of the Faculty of Science and Licella CEO Dr. Len Humphreys created Licella, which has received 14 years of funding from the University of Sydney. The mixed garbage will be transported on a conveyor belt, where robots will recognize it based on the procedure they have explained. After that, the robots will divide them into various streams for further processing. As a result, shredding, grading, and preparation may be used to create fuel and chemical compounds, which could be used to make polymers for packaging or indoor-outdoor furniture or signs.
“This highly innovative materials handling process can help extend the range of the Cat-HTR conversion technology to now include increasingly challenging waste streams, highlighting the benefit of close industrial and academic collaboration,” said Professor Maschmeyer.
Soft plastics could previously only be sorted by humans, thus the system created by the team will be considerably more cost-effective and efficient in terms of cost and production. Robots, for example, can make 2000 choices every hour, but humans can only make 800. It’s also a system that’s a lot more scalable. Because the system’s major components are built-in software that can be readily deployed, it is scalable.
Information Sources: