When subjected to particular conditions, such as heat, light, or other external stimuli, self-healing plastics have the potential to mend damage or cracks naturally. Chemists create mineral polymers with a variety of beneficial qualities from sustainable fundamental building blocks, and biologists demonstrate the material’s superior microbiological degradability.
Imagine a plastic that is harder than current plastics, non-flammable, and even self-healing. But wait, there’s more! It may be manufactured at room temperature in water, which saves energy and eliminates the need for harmful solvents. You can mould the plastic in whatever way you like before it hardens, just like chewing gum. It can also be turned back to its “chewing gum” form at any moment by adding water, reshaped, and therefore recycled as many times as required.
Is that even possible? No, it doesn’t! A mineral plastic was presented in 2016 by a research team led by Konstanz scientist Helmut Cölfen. Despite the fact that the plastic, with its new manufacturing technique and remarkable material qualities, has since piqued the interest of industry, the Konstanz chemists saw a critical shortcoming: it was difficult to biodegrade due to its chemical composition.
Our new mineral plastic has the same positive properties as the previous one, but has the decisive advantage that its basic building block – polyglutamic acid – can be produced with the help of microorganisms and is completely biodegradable.
Helmut Cölfen
A new ingredient for greater environmental compatibility
“Previously, we produced our mineral plastic with polyacrylic acid.” Chemically, this acid has the same backbone as polyethylene, which is known to pose serious environmental difficulties due to its low biodegradability,” adds Cölfen. The study team, coordinated by Cölfen and Ilesha Avasthi, a postdoctoral researcher in Cölfen’s lab, set to work looking for an alternative basic building block to make an environmentally friendly mineral plastic that keeps the interesting features of the original material. They discovered what they were looking for.
The Konstanz chemists report the latest generation of their mineral plastic in the journal Small Methods. Polyglutamic acid is being used in place of petroleum-based chemicals such as polyacrylic acid. This natural biopolymer is widely available and can even be obtained sustainably, for example, by biotechnological manufacture utilising microorganisms. Polyglutamic acid can be degraded by a wide range of naturally occurring microbes.
“Our new mineral plastic has the same positive properties as the previous one, but has the decisive advantage that its basic building block – polyglutamic acid – can be produced with the help of microorganisms and is completely biodegradable,” explains Helmut Cölfen.
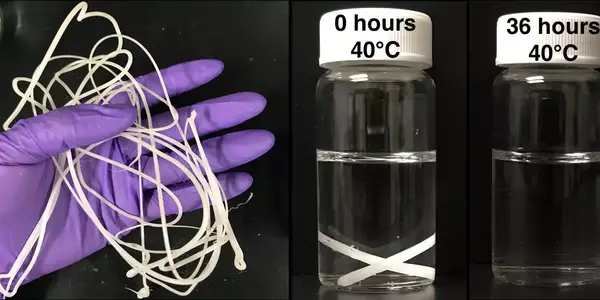
Support from biologists
Biodegradable plastics are those that can be broken down by natural processes into harmless substances, usually with the help of microorganisms, within a reasonable timeframe. Combining the self-healing capability with biodegradability would be a significant advancement, as it would create a more sustainable and environmentally friendly material.
To demonstrate that this biodegradability extends beyond the individual components of the novel crystalline plastic, the chemists engaged the help of David Schleheck and postdoc Harry Lerner from the Department of Biology at the University of Konstanz. “In his laboratory, Helmut Cölfen created a new type of mineral plastic, and our task now was to make it disappear with the help of microorganisms,” Schleheck explains with a smile.
The biologists were able to demonstrate in degrading trials that microorganisms found in forest soils, for example, began metabolising the mineral plastic after only a few days. The microbes had totally destroyed the plastic after only 32 days. So the researchers have actually succeeded in making the mineral plastic with all its positive material properties now also sustainable and biodegradable.