Combustors are critical components of gas engines and the chambers where the combustion that powers the engine takes place. However, combustors frequently fail as a result of lethal high-frequency oscillations during the combustion process.
Combustors – the chambers in which the combustion that powers the engine occurs – are a critical component of gas engines that can fail due to fatal high-frequency oscillations during the combustion process. Researchers have discovered what causes them to use advanced time-series analyses based on complex systems, opening up new avenues for solving the problem.
Contained combustion systems, which are essentially combustion chambers, are found in rocket engines. Nonlinear interactions between turbulent fuel and oxidizer flow, sound waves, and heat produced by chemical reactions cause an unstable phenomenon known as ‘combustion oscillations’ in these chambers. The force of these oscillations on the body of the combustion chamber – the mechanical stress on the chamber is great enough to threaten the engine’s catastrophic failure. What is the source of these oscillations? The solution has yet to be discovered.
In a breakthrough published in Physics of Fluids, a team led by Prof. Hiroshi Gotoda, Ms. Satomi Shima, and Mr. Kosuke Nakamura from Tokyo University of Science (TUS), in collaboration with Dr. Shingo Matsuyama and Dr. Yuya Ohmichi from the Japan Aerospace Exploration Agency (JAXA), used advanced time-series analyses based on complex systems to find out.
A team of researchers from Tokyo University of Science, Japan, and the Japan Aerospace Exploration Agency used advanced time-series analyses based on complex systems to find out the cause of fatal problems in rocket engine combustors.
Prof. Gotoda explains their work, “Our main goal was to reveal the physical mechanism behind the formation and maintenance of high-frequency combustion oscillations in a cylindrical combustor using sophisticated analytical methods inspired by symbolic dynamics and complex networks.” The American Society of Physics covered these findings in their news section, as did the Institute of Physics on their news platform Physics World.
The scientists chose a model rocket engine as the combustor to simulate. They were able to pinpoint and visualize the transition from the stable combustion state to combustion oscillations. They discovered that significant periodic flow velocity fluctuations in fuel injectors affect the ignition process, causing changes in heat release rate. The fluctuations in the heat release rate synchronize with the fluctuations in the pressure inside the combustor, and the cycle continues in a series of feedback loops that sustain combustion oscillations.
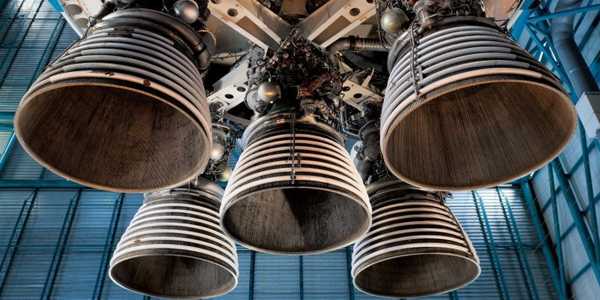
Contained combustion systems, which are typically combustion chambers, are used in rocket engines. Nonlinear interactions in such chambers, together with turbulent fuel and oxidizer flows, sound waves, and heat generated by chemical reactions, produce a volatile phenomenon known as “combustion oscillations.”
The force of such oscillations on the body of the combustion chamber—the mechanical stress produced on the chamber—is sufficient to cause the engine to fail catastrophically. The mystery of what causes such oscillations remains unsolved.
Furthermore, by examining a spatial network of pressure and heat release rate fluctuations, the researchers discovered that clusters of acoustic power sources form and collapse on a regular basis in the shear layer of the combustor near the injection pipe’s rim, contributing to the combustion oscillations.
These findings, while specific to liquid rocket engines, provide reasonable explanations for why combustion oscillations occur. Prof. Gotoda elaborates, “Combustion oscillations can be fatal to combustors in rocket engines, aero engines, and gas turbines used to generate electricity. As a result, understanding the mechanism of combustion oscillation formation is an important research topic. Our findings will help us better understand the mechanism of combustion oscillations in liquid rocket engines.”
Indeed, these findings are significant and can be expected to open doors to novel routes of exploration to prevent combustion oscillations in critical engines.
The two most important requirements placed on a rocket combustor are performance and life. Cost and reliability concerns are driving the development of new designs that use new materials in potentially new cycles. Although the aerospace industry has traditionally relied heavily on derivative designs for new systems, there is a scarcity of design heritage for propulsion systems that can meet these life and cost objectives. Furthermore, running a development program for large engines on full-scale hardware is prohibitively expensive. As a result, the need for accurate design analysis models is greater than ever.