Friction control is critical in a wide range of applications, from small-scale devices to large-scale industrial systems. At various scales, there are several methods for managing and manipulating friction.
Friction is difficult to predict and control, especially because surfaces in contact are rarely perfectly flat. New experiments show that the amount of friction between two silicon surfaces is determined, even at large scales, by the formation and rupture of microscopic chemical bonds between them. This allows surface chemistry techniques to be used to control the amount of friction. The new findings have been published in Physical Review Letters.
“There is a lack of quantitative understanding of friction, despite its critical role in addressing challenges as diverse as earthquake prediction and energy consumption in mechanical devices,” says PhD researcher Liang Peng, who led the study. This is no small matter: friction is thought to account for more than 20% of global energy consumption. Controlling friction in machinery is also critical for reducing material wear and improving positioning precision.
Our result is quite remarkable because it demonstrates a quantitative understanding of macroscopic friction from first principles. Our findings can thus bridge the knowledge gap that is impeding understanding-based friction control.
Liang Peng
Peng collaborated with researchers from the University of Amsterdam’s Institute of Physics and Van ‘t Hoff Institute of Molecular Sciences, as well as the Advanced Research Center for Nanolithography (ARCNL). The study is part of an ongoing investigation into how large-scale friction emerges at the microscopic level.
In recent years, new research methods have allowed scientists to hone in on exactly what happens when two surfaces collide and slide over one another. Most importantly, surfaces are never perfectly smooth. They appear to be mountainous landscapes with pronounced peaks and valleys at the scale of a nanometre, one billionth the size of a metre. Previous experiments and numerical simulations have shown that friction is largely determined at this small scale by the formation and rupturing of bonds between surface atoms. This is influenced not only by the roughness of the sliding surfaces, but also by the presence of atoms or molecules (such as water) at the interface.
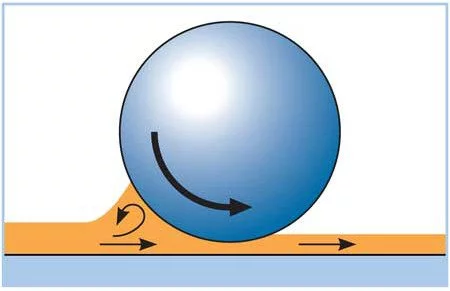
“We decided to extend and apply these nanofriction mechanisms to larger, industrially relevant scales,” explains Peng. Using a special instrument called a rheometer, the researchers studied how the amount of friction between a relatively rough silicon ball and a smooth silicon wafer depends on the density of microscopic chemical bonds at the interface. Silicon, with chemical symbol Si, is a particularly interesting material to study thanks to its widespread use in the semiconductor industry. Its abundance in the Earth’s crust also makes it relevant to the study of earthquakes.
After cleaning the surfaces, the researchers discovered that when the surfaces are dried in pure nitrogen gas for a longer period of time, much less force is required to slide the ball over the wafer – in other words, there is less friction. Experiment after experiment revealed what happens at the atomic level: longer drying reduces the number of hydroxyl (OH) groups exposed at the silicon surface. When these groups come into contact with another silicon surface, they combine to form silicon-oxygen-silicon (Si-O-Si) bonds between the two surfaces.
The study demonstrates that there is a striking relationship between the friction force measured at large scales and the density of microscopic Si-OH groups present on the two silicon surfaces before contact, which controls the number of Si-O-Si bonds formed during contact. The density of these chemical bonds is controlled by adjusting the drying time of the cleaned surfaces. This means that the friction force between silicon surfaces can now be predicted and controlled.
“Our result is quite remarkable because it demonstrates a quantitative understanding of macroscopic friction from first principles. Our findings can thus bridge the knowledge gap that is impeding understanding-based friction control,” Liang concludes.