A wind turbine converts wind energy into electricity by utilizing the aerodynamic force of the rotor blades, which function similarly to an airplane wing or helicopter rotor blade. When the wind blows across the blade, the air pressure on one side of the blade drops. The differential in air pressure between the two sides of the blade generates both lift and drag. The force of the lift is greater than the force of the drag, causing the rotor to spin. The rotor is connected to the generator either directly or via a shaft and a series of gears, which speeds up the rotation and allows for a physically smaller generator. The conversion of aerodynamic force to generator rotation generates power.
Wind turbines generate 4% of the world’s energy, yet they only work when the wind is blowing just right. Scientists have discovered a way to make wind turbine blades 35% more efficient at producing electricity by pulling inspiration from the flexible wings of insects. If realized, this green technology could become a more feasible alternative to fossil fuels in the future years.
Scientists demonstrate that combining aspects of a seagull’s wing with an engineered flow control attachment is known as a Gurney flap can significantly improve wind turbine performance. The scientists simulated the employment of the combined flow control accessory in a range of settings, including the high and low angle of attack and pre-and post-stall scenarios, to get the optimal aerodynamic performance. They compared their computational simulations to experimental results for a dynamic stalling aircraft wing.
The overall trend of the computed lift curve agrees well with the experimental measurement data. Because the dynamic stall and its control are famously difficult to forecast, our simulation accuracy is deemed adequate.
Xiaomin Liu
Wind energy is based on efficient wind turbine blades that act as airfoils, which are structures similar to an airplane wing. Airflow control accessories, similar to those found in aircraft, improve the aerodynamic performance of the turbine blade.
Scientists from China demonstrate in the Journal of Renewable and Sustainable Energy, published by AIP Publishing, how a bionic method combining elements of a seagull’s wing with a manufactured flow control device is known as a Gurney flap may considerably improve wind turbine performance.
A Gurney flap is a tiny tab that projects at right angles from a wing’s trailing edge. Its presence disrupts wind flow patterns and improves performance at low angles of attack in particular. The angle of attack in aerodynamics is the angle formed by a line passing through the center of an aircraft wing and the approaching flow of air.
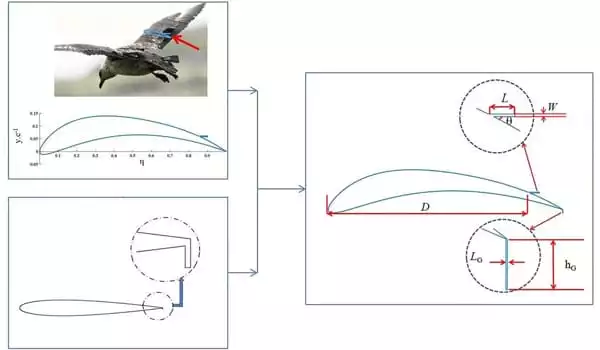
Although Gurney flaps improve airfoil performance at low attack angles, they are not optimal at high attack angles. According to research, while Gurney flaps can greatly improve wind turbine performance in specific instances, the turbine speed would be reduced.
Bionic flow control is a new method that mimics biological flight control systems, such as wings and feathers. The concept stems from the observation that when a bird lands or is caught in a burst of wind, the feathers on the top of its wings pop out, forming a natural flap.
Bionic feather-inspired flaps can improve lift and delay the onset of stalling at high angles of attack, according to computational and experimental investigations. Despite their benefits, adding bionic flaps can limit lift, especially before a stall occurs. As a result, the researchers tried a method that combined Gurney flaps with bionic characteristics.
To get the optimal aerodynamic performance, the scientists simulated the operation of the combined flow control accessory in a range of circumstances, including the high and low angle of attack and pre-and post-stall scenarios. They compared their computational simulations to experimental results for an airplane wing experiencing a dynamic stall.
“The overall trend of the computed lift curve agrees well with the experimental measurement data. Because the dynamic stall and its control are famously difficult to forecast, our simulation accuracy is deemed adequate” Xiaomin Liu, the author, stated.
According to Liu, the combined flow control accessory efficiently enhances the airfoil’s lift coefficient. “When a combination of Gurney flap and the bionic flap is employed at angles of attack ranging from 16 to 24 degrees, the maximum lift coefficient of the airfoil is raised by 15%.”