Zirconium carbide (ZrC) is an exceedingly hard refractory ceramic material that, due to its exceptional qualities, is one of the most appealing ultrahigh-temperature ceramics. Commercially, it’s employed in cutting tool bits, and it’s commonly treated by sintering. It has a gray metallic powder look and a cubic crystal structure. It has a gray metallic powder look and a cubic crystal structure. It has a high level of corrosion resistance. This interstitial transition-metal carbide from Group IV is also found in ultra-high temperature ceramics (UHTC).
Electrospinning and pyrolysis of a novel polymeric precursor, polyzirconosaal (PZSA), were used to make ZrC nanofibers, with the inclusion of polyvinylpyrrolidone (PVP) as a spinning aid. It is a possible coating, oxygen-gettering, or inert matrix material for advanced high-temperature nuclear applications due to its exceptional high-temperature mechanical capabilities, great electrical and thermal conductivity, high melting point, and great chemical resistance.
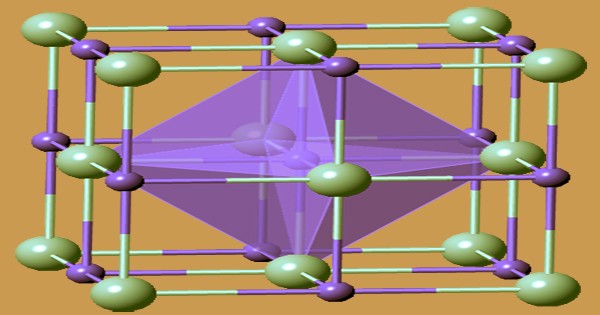
ZrC exhibits a thermal conductivity of 20.5 W/mK and an electrical conductivity (resistivity 43 cm) that are similar to zirconium metal due to the existence of metallic bonding. The fibrous shape of the ZrC nanofibers produced was outstanding. Nanoscale ZrC particles were found scattered in the fibers containing free carbon in the microstructures.
In nuclear reactors, hafnium-free zirconium carbide can be utilized as a refractory coating. It can be used to coat uranium dioxide and thorium dioxide nuclear fuel particles due to its low neutron absorption cross-section and low damage sensitivity under irradiation. This material has a high melting point (3530 °C), modulus (~440 GPa), and hardness due of the strong covalent Zr-C bond (25 GPa). When compared to other carbides such as WC (15.8 g/cm3), TaC (14.5 g/cm3), or HfC (12.67 g/cm3), ZrC has a lower density (6.73 g/cm3).
Using the Debye-Scherrer technique, the average crystallite size of ZrC particles was 42 nm. X-ray diffraction (XRD), SEM, and TEM were used to analyze the ZrC nanofibers. ZrC appears to be ideal for application in re-entry vehicles, rocket/scramjet engines, or supersonic vehicles where load-bearing capabilities at low densities and high temperatures are critical criteria. ZrC is being studied as a structural and fission product barrier coating material for TRISO (tri-isotropic) coated nuclear fuel used in high temperature reactors (HTRs), either in place of or in addition to silicon carbide (SiC).
Zirconium carbide, like most refractory metal carbides, is sub-stoichiometric, meaning it contains carbon vacancies. The structure of ZrC fibers is effectively preserved, and nanosized hexagonal ZrC crystals are scattered throughout the fibers. The material contains free carbon at carbon concentrations greater than ZrC0.98. For carbon-to-metal ratios ranging from 0.65 to 0.98, ZrC is stable. In the metallurgical, chemical, aerospace, energy, and aviation industries, nanometer zirconium carbide can be used in hard alloy, nano-structured parts and devices. It can be employed in novel insulation thermostat texts, reformed naylon, and functional fiber that absorbs and saves heat energy.
An important cermet substance is a combination of zirconium carbide and tantalum carbide. Zirconium carbide can be made in a variety of ways. The carbothermic reaction of zirconia with graphite is one technique. Solution-based processing can also be used to make zirconium carbide. Refluxing a metal oxide with acetylacetone achieves this. Chemical vapor deposition is another way of manufacturing. This is accomplished by passing halide gas through a zirconium sponge that has been heated.
ZrC is utilized as a surface coating for metals and other materials, in the manufacture of metal matrix, ceramic matrix, and polymer nanocomposites, as sintering additives, and as grain refining agents or nucleating agents in composite materials. It also has a high emissivity and current capacity at high temperatures, making it a viable material for thermo-photovoltaic radiators, as well as field emitter tips and arrays. It’s also utilized as an abrasive, in cladding, cermets, incandescent filaments, and cutting tools, among other things.
Information Sources: