Masonry Reinforcement, its Types and Accessory Metals for Masonry Structure
Masonry reinforcement and accessories includes:
- Steel reinforcement
- Connectors
- Sealants
- Flashings
- Coatings
- Vapor and moisture barriers
Steel Reinforcement for Masonry Structure
Reinforcing bars, joint reinforcement, and deformed reinforcing wire are all types of steel reinforcement used in masonry structures. Steel bars are used to increase the masonry structure’s tension and compression strengths. While reinforcement bars are used in masonry columns to boost their compression strength, steel reinforcement is added to masonry bond beams, lintels, and walls to improve the tensile strength of the member. A masonry construction uses hot-rolled deformed bars with ribs on their surface to increase bond strength.
As per ACI 530.1-11, the maximum reinforcement steel bar size is No.11. The performance of the masonry structure and established construction practice determine the size constraint for reinforcing bars. It is asserted that using and dispersing small-size steel bars in brickwork offers superior performance compared to sparingly using large-size reinforcements.
The minimum yield stress of the steel used to make the steel reinforcement bars is typically used to categorize the steel reinforcement bars. When corrosion-protected reinforcement is provided as per the design, steel bars with epoxy coating or zinc coating may be used in masonry buildings. Epoxy and zinc coatings both shield steel bars from harsh elements and so lengthen the life of the construction. If steel bars are coated with epoxy, their development length must be increased and must be 1.5 times longer than that of uncovered bars.
On the other hand, since zinc offers the same properties as uncoated bars, zinc-coated bars do not require a longer development period. It should be noted that coated bar transport and installation require careful attention to prevent coating damages, failing which the steel coating’s intended function will not be served. Therefore, any steel coating damage must be fixed before installation.
In masonry buildings, fiber-reinforced polymer bars can be used in place of zinc and epoxy-coated bars in harsh situations. The fact that the FRP bar comes in a variety of sizes and is very light reduces the cost of delivery, handling, and installation, which is favorable.
Three types of joint reinforcement exist, including welded wire fabric, deformed reinforcing wire, and ladder- or truss-type joint reinforcement. Joint reinforcement is used for a variety of purposes, including controlling differential movements, expanding the size of a panel, and increasing the distance between movement joints. It also enhanced horizontal bending and limited cracks in masonry structures, in addition to other benefits.
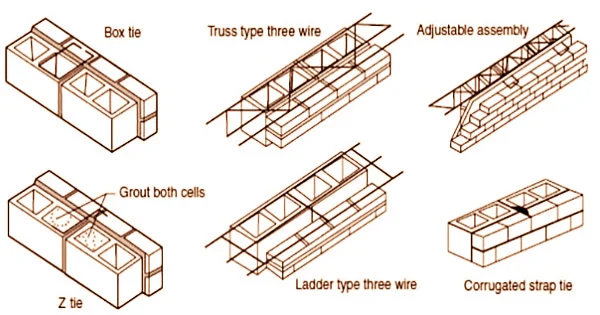
Connectors for Construction of Masonry Structures
There are various types of connectors that are used to connect or secure two members or parts together. For instance, ties can join two Wythe’s of masonry wall together and adjustable ties may be employed to make rooms for differential elevation in masonry bed joints.
Sealants in Masonry Walls
Sealants are used to fill and seal any gaps or joints purposefully made in masonry walls for certain objectives. Building joints, expansion joints, and control joints are the three main types of joints found in masonry construction. Sealants are typically made from synthetic polymers like butyl rubber, silicone, latex, and neoprene. The ratio of the minimum thickness to the original thickness determines the elastic property of the sealant, which includes compressibility.
Deteriorated sealants must be replaced with new ones in accordance with the expected service life of the sealants. According to claims, the majority of sealants that are applied to exterior walls or faces typically last seven years. Sealant exposure to ozone and ultraviolet radiation is the primary cause of sealant breakdown. This is due to the fact that such circumstances
Flashings for Construction of Masonry Walls
Flashing is a flexible and adaptable material that is watertight and can be made of copper, stainless steel, plastic, aluminum that has been covered with plastic, and rubberized asphalt. Compared to plastic flashing that is prone to tearing, metallic flashing has a far longer life span. The masonry-adhering rubberized asphalt flashing is simple to apply and exhibits reasonable durability.
Masonry walls have flashings built in a variety of places, including all interrupted drainage cavities, the base of each story level, under window and door sills, and over window and door lintels. It is used to drain water that seeps into the masonry wall’s exterior Wythe. Weep holes should be spaced 61 cm or so above the flashing level.
Coatings for Masonry Structures
Masonry structure Paints and water-repellent coatings are applied during coating. When compared to water repellent coatings, the effect of a water repellent admixture is superior. The latter cannot fill in very wide cracks; instead, it traps water behind them, which causes harm to the coating behind it as a result of freezing and thawing.
Vapor and moisture barriers for Masonry Structures
A vapor barrier is a waterproof membrane used to stop vapor or water from penetrating brick walls. This prevents interstitial condensation from occurring inside the drainage wall’s air gap. The vapor membrane is used for the exterior face of the inner Wythe wall in warm conditions whereas it is applied for the interior surface of the outer Wythe in cold conditions. This is because warm air around the structure can go through the outer Wythe and condense within the inner Wythe while in cold conditions warm air inside the building will pass through inner Wythe and condense in the cavity.
Vapor barriers are practically applied to the outer face of the inner Wythe. The moisture barrier prevents vapor from penetrating the masonry wall but not water, allowing condensation to form in the drainage wall’s air space.